Ayse KALEMTAS*
Department of Metallurgical and Materials Engineering, Bursa Technical University, 16310 Bursa, Turkey
Corresponding Author’s Email: ayse.kalemtas@btu.edu.tr
DOI : http://dx.doi.org/10.13005/msri/160206
Article Publishing History
Article Received on : 01-July-2019
Article Accepted on : 06-Aug-2019
Article Published : 10 Aug 2019
Plagiarism Check: Yes
Reviewed by: Fatma Ozutok
Second Review by: Chandra Mohan
Final Approval by: Dr. Ozan Toprakci
Article Metrics
ABSTRACT:
In this study, kaolin bonded alumina-alginate composite beads were fabricated via a facile one-step sol-gel process by using sodium alginate. In order to achieve sintering of the beads at lower sintering temperatures a limited amount of CC31 commercial-grade kaolin was used as a sintering additive (Al2O3:CC31 commercial-grade kaolin=14:1). Produced composite beads were heat treated at 1300°, 1400° and 1500°C for 1 hour to achieve partial densification of the beads. TG-DTA analysis of the CC31 commercial-grade kaolin showed that mullite phase formation took place approximately at 1000°C. However, XRD measurements revealed that there is only alumina phase in the sintered ceramic beads. Due to the low amount of CC31 commercial-grade kaolin, mullite formation was not detectable via XRD analysis. No significant grain growth was observed at the sintered samples depending on the increasing sintering temperature. However, when the sintering temperature was increased, densification ratio and mechanical properties of the produced beads were enhanced significantly. Microstructural investigations of the sintered beads shown that with the help of the liquid phase sintering process, a good chemical bonding was achieved between the alumina particles.
KEYWORDS:
Alumina; Kaolin; Low-Temperature Synthesis; Porous Ceramic Beads
Copy the following to cite this article:
KALEMTAS A. Effect of the sintering temperature on the fabrication of alumina beads. Mat. Sci. Res. India;16 (2).
|
Copy the following to cite this URL:
KALEMTAS A. Effect of the sintering temperature on the fabrication of alumina beads. Mat. Sci. Res. India;16 (2). Available from: http://bit.ly/2yNN203
|
Introduction
Porous alumina ceramics have attracted a significant attention due to their good thermal stability even at elevated temperatures, constructive surface properties, chemical stability, and relatively high strength.1-10 Porous alumina ceramic materials are widely used for many applications such as catalyst supports,11-13 bone tissue engineering,14-16 membrane,17-19 high temperature filtration,20 water desalination21-23 diesel particulate filters24 and as an anodic oxide coating in tools.19, 25, 26 Recently ceramic microspheres either in the form of dense, hollow, and porous structures are very attractive materials. Owing to their unique characteristic properties such as high porosity, low density, mechanically and thermally stable structure, and providing an opportunity to use economical materials.27-29 Highly porous ceramic materials can be achieved in many different ways such as using fugitive additives,30-32 partial sintering,2, 30, 32-34 polymeric sponge,20, 35, 36 etc. Using fugitive materials such as starches,20, 30, 31 saw dust,37, 38 and carbon black,39-41 provide high open porosity and facilitate achieving highly interconnected porosity.
Ceramic-based microspheres can be used for various applications such as drug delivery, hard tissue regeneration, radiant burners, acoustic insulations, catalyst support, thermostable materials, filters, as reinforcement for foams for the structural applications, and sorbent materials.42-44 These microspheres have been used in many industrial applications in combination with a different type of materials. Fabrication of hollow/porous ceramic microspheres is carried out via various processing techniques such as template,45-48 multi-template,49 hydrothermal processing,50, 51 spray drying,52-54 sonochemical,49 solvothermal process,55-57 pseudomorphic synthesis,58 emulsion microencapsulation,59 sacrificial core,60-62 emulsion evaporation63, 64 nozzle reactor and microwave-assisted solvothermal synthesis.65 Porous alumina ceramic beads can serve as an ideal filtration material due to its highly porous structure, controlled pore size, and distribution as well as its rigid structure.
In the current work, kaolin bonded alumina porous beads were fabricated via a facile, eco-friendly, and convenient route by using sodium alginate as an in situ gelling templates. A huge amount of investigations has been reported in literature dealing with the effects of the process parameters on the vibrational droplet technology in alginate systems. However, studies on the fabrication of high alumina ceramic loaded vibrational droplet technology is very limited. Alumina has a high melting temperature; thus solid-state sintering needs very high sintering temperatures and dwell times. In order to achieve partial sintering of alumina beads at low sintering temperatures in this study, a limited amount of CC31 commercial-grade kaolin was used as a sintering additive (Al2O3:CC31 commercial-grade kaolin=14:1). Effect of the sintering temperature (1300°-1500°C) on the densification of the kaolin bonded porous alumina beads were investigated for the first time. It was determined that when the sintering temperature was ³ 1400°C, the strength of the spherical ceramic beads significantly increased.
Experimental Procedure
CC31 commercial-grade kaolin (Esan Eczacibasi Group, Turkey) was used as a sintering additive to enhance densification of the Al2O3 (Esan Eczacibasi Group, Turkey) ceramic beads at relatively low temperatures. As-received kaolin powder content given by the manufacturer was Al2O3 (35.4 wt%), SiO2 (50.7 wt%), K2O (2.4 wt%), MgO (0.5 wt%), Fe2O3 (0.6 wt%), CaO (0.3 wt%) and Na2O (0.5 wt%) with an ignition loss of 9.5 wt%. Al2Si2O5(OH)4 is the empirical formula for kaolinite. Theoretical chemical composition of the kaolinite is Al2O3, 39.50 %; SiO2, 46.54 %; and H2O, 13.96%. Thermal behavior of the CC31 commercial-grade kaolin in air atmosphere was investigated via thermogravimetry (TG) and differential thermal analysis (DTA) in a simultaneous TG/DTA analyzer (Netzsch STA 449F3) at a heating rate of 10°C/min.
Bead production was carried out with the following procedure. Six grams of sodium alginate (SA) (Katki Dunyası, Turkey) was dissolved in 200 mL distilled water by magnetic stirring at room temperature for 24 hours. A homogenous slurry containing 70 g Al2O3, 5 g CC31 and 150 mL SA solution, was prepared in a planetary ball mill at a rotation speed of 350 rpm for 45 minutes. The cross-linking solution was prepared via dissolving 1 wt.% calcium chloride (CaCl2, Katki Dunyası, Turkey) in distilled water by magnetic stirring at room temperature for 1 hour. Prepared aqueous SA + ceramic solution was added dropwise into CaCl2 aqueous solution at room temperature using a 60 mL hypodermic syringe through a needle under constant stirring at room temperature. The alginate−ceramic composite beads are formed via cross-linking in the CaCl2 solution for at least 30 minutes. Then beads are removed from the solution via sieving and washed with distilled water for many times. Fig. 1 displays fabricated Al2O3−kaolin−alginate green composite beads and sintered beads. Macroscopic investigations depicted that the spherical beads kept their shape during the sintering process (Fig. 1-b).
Figure 1: (a) Al2O3−kaolin−alginate green composite beads, and (b) alumina ceramic beads, produced via sintering at 1400°C for 1 hour.
Al2O3−kaolin−alginate green composite beads were sintered at 1300°, 1400° and 1500°C for 1 hour with a 10°C/minute heating and cooling rate. Microstructural development of the alumina beads were investigated with scanning electron microscopes (SEM, Carl Zeiss/Gemini 300 and Tescan Vega3) in a secondary electron (SE) image mode. Elemental composition of the grain boundaries were investigated via an energy dispersive X-ray spectrometer (EDX, Bruker). Phase identification of the samples were performed by X-ray diffraction (XRD, Bruker AXS/Discovery D8), using monochromatic Cu-Kα radiation (l=1.5406Å).
Results and Discussion
Densification of alumina ceramics via solid state sintering requires very high temperatures. Thus CC31 commercial-grade kaolin was used as a liquid phase sintering aid to decrease the sintering temperature of the alumina-based ceramic beads. XRD analysis of the as-received CC31 commercial-grade kaolin revealed that kaolinite, illite, and free quartz phases exist in the powder (Fig. 2-a). Microstructural investigation of the CC31 commercial-grade kaolin revealed that the particle size of the kaolin is very fine (Fig. 2-b). To avoid exaggerated grain growth Al2O3:CC31 commercial-grade kaolin weight ratio was kept constant as 14:1.
Figure 2: (a) XRD pattern, and (b) microstructure of the CC31 commercial−grade kaolin.
Stability and thermal behavior of the sintering aid was determined by simultaneous thermogravimetric and differential thermal analysis (TG-DTA). TG-DTA results of the CC31 commercial-grade kaolin (Fig. 3) revealed that desorption of the water took place at low temperature. The endothermic peak, determined at 74.7°C represents the removal of the absorbed water. The endothermic peak observed at 547.4°C represents dehydration of the kaolin. The exothermic peak observed at 1001.2°C represents the formation of the mullite phase. Mullite formation temperature is determined as 980°C in a study carried out by Chakraborty and Ghosh.66 Chen et al.,67 reported this exothermic mullite formation reaction temperature as 1006.5°C. In the literature kaolin to mullite reaction series have been intensively investigated. It is reported that the reaction temperatures can change depending on various parameters. Particle size and distribution of the kaolin, source of the kaolin, the crystallinity of kaolin, heating rate, and impurity content can change the reaction temperatures. 68-85 Depending on the decreased particle size of the kaolin, also reaction temperatures are decreased. The impurity content of the kaolin considerably affects the composition and rheological properties of the liquid phase in the system which mullite formation takes place in it. The impurity content has a significant effect on the kaolin to mullite reaction series.
Figure 3: TG/DTA simultaneous analysis result of the CC31 commercial-grade kaolin.
Phase analysis of the monolithic CC31 commercial-grade kaolin sintered at 1300°, 1400° and 1500°C depicted that kaolin to mullite reaction series were completed in all these temperatures. Mullite phase was detected in all samples (Fig. 4).
Figure 4: XRD patterns of the CC31 commercial−grade kaolin sintered at (a) 1300°C, (b) 1400°C and (c) 1500°C for 1 hour.
Kaolin to mullite reaction series can be explained by the following reactions:
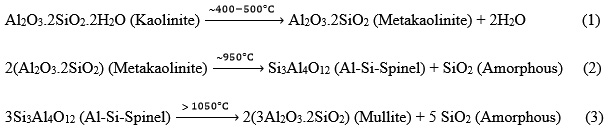
Fracture surface microstructure investigations of the alumina beads densified via liquid phase sintering at different sintering conditions are given in Fig. 5. Depending on the sintering temperature densification ratios of the samples are slightly changed. Porosity amount and pore size decreased with the increased sintering temperature. SEM investigations confirmed that the highest densification ratio was achieved at 1500°C for 1 hour. When the sintering temperature of the beads was ³ 1400°C, it was observed that the strength of the ceramic beads increased significantly due to enhanced densification ratio. Macroscopic and microscopic investigations revealed that the morphology of the ceramic beads did not change during the sintering step (Fig. 1-b and 5-c). As clearly observed in Fig. 5-b, with the help of liquid phase sintering process a good chemical bonding was achieved between the alumina particles.
Figure 5: Scanning electron microscopy images of kaolin bonded alumina beads produced via sintering at (a, b) 1300°C, (c, d) 1400°C, and (e) 1500°C for 1 hour.
EDX analysis of the sample sintered at 1400°C for one hour is given in Fig. 6. The chemical analysis of the grain boundary phases revealed that there is some silicon and sodium at the grain boundary phases due to CC31 commercial-grade kaolin sintering aid.
Figure 6: (a) Investigated region (shown as “Spectrum 1”), and (b) the corresponding EDX spectra achieved for “Spectrum 1” point and the associated element quantification.
XRD results of the kaolin bonded alumina beads revealed that the beads contain alumina phase. There is only a very small peak (showed with a red arrow in Fig. 7) which belongs to mullite phase. Mullite phase forms in the sample as an in-situ phase via the reactions of kaolin at elevated temperatures. However, the beads contain a very low amount of kaolin (alumina:kaolin weight ratio is 14:1); thus the formation of mullite phase is also very low. As a result, detection of the mullite phase in the samples via XRD is not accurately possible.
Figure 7: X-ray diffraction patterns of the (a) Al2O3 powder, and ceramic beads produced via sintering at (b) 1300°C, (c) 1400°C, and (d) 1500°C for 1 hour.
Conclusion
- Kaolin bonded alumina porous ceramic beads were produced via a facile, eco-friendly, and convenient route by using sodium alginate as an in situ gelling template for the shaping process and partial sintering for the densification.
- Macroscopic and microscopic investigations revealed that the shape of the produced alumina beads did not change significantly during the sintering step and spherical sintered alumina beads were achieved.
- Sintering studies were carried out between 1300°-1500°C. When the sintering temperature of the beads was ³ 1400°C it was noticed that strength of the spherical ceramic beads significantly increased due to enhanced liquid phase sintering process.
- Produced porous alumina ceramic beads can be promising materials for various applications such as desalination, water treatment, refractory applications, and a versatile reinforcement for the different polymer, metal or ceramic matrix composite structures.
Acknowledgments
The author gratefully acknowledges to Ceramic Research Center (Eskisehir, Turkey) for TG-DTA analysis of kaolin, BUTAL (Bursa Test and Analysis Laboratory, Bursa, Turkey) for the SEM investigations of the alumina ceramic beads and Bursa Technical University Central Research Laboratory (Bursa, Turkey) for the XRD and SEM-EDX analysis.
Funding source
The author declares that the funding is done by the author only.
Conflict of Interest
The authors have no conflicts of interest to disclose.
References
- Z.Y. Deng, T. Fukasawa, M. Ando, G.J. Zhang, T. Ohji, Microstructure and mechanical properties of porous alumina ceramics fabricated by the decomposition of aluminum hydroxide, Journal of the American Ceramic Society. (2001); 84(11): 2638-2644.
CrossRef
- E. Gregorová, W. Pabst, V. Nečina, T. Uhlířová, P. Diblíková, Young’s modulus evolution during heating, re-sintering and cooling of partially sintered alumina ceramics, Journal of the European Ceramic Society (2019); 39(5): 1893-1899.
CrossRef
- L. Fu, A. Huang, H. Gu, H. Ni, Fabrication of lightweight alumina containing fine closed pores by controlling the relationship between phase stress and superplasticity: Experimental and mathematical studies, Ceram Int. (2018); 44(16): 20034-20042.
CrossRef
- L. Fu, A. Huang, H. Gu, H. Ni, Properties and microstructures of lightweight alumina containing different types of nano-alumina, Ceram Int (2018); 44(15): 17885-17894.
CrossRef
- Q. Wang, Y. Li, S. Li, R. Xiang, N. Xu, S. OuYang, Effects of critical particle size on properties and microstructure of porous purging materials, Materials Letters (2017); 197: 48-51.
CrossRef
- T. Uhlířová, V. Nečina, W. Pabst, Modeling of Young’s modulus and thermal conductivity evolution of partially sintered alumina ceramics with pore shape changes from concave to convex, Journal of the European Ceramic Society (2018); 38(8): 3004-3011.
CrossRef
- G. Rajeev, B.P. Simon, L.F. Marsal, N.H. Voelcker, Advances in Nanoporous Anodic Alumina‐Based Biosensors to Detect Biomarkers of Clinical Significance: A Review, Adv Healthc Mater (2018); 7(5).
CrossRef
- S. Said, S. Mikhail, M. Riad, Recent progress in preparations and applications of meso-porous alumina, Materials Science for Energy Technologies (2019).
CrossRef
- Z. Fohlerova, A. Mozalev, Tuning the response of osteoblast-like cells to the porous‐alumina‐assisted mixed‐oxide nano‐mound arrays, Journal of Biomedical Materials Research Part B: Applied Biomaterials (2018); 106(5): 1645-1654.
CrossRef
- J.F. Poco, J.H. Satcher, L.W. Hrubesh, Synthesis of high porosity, monolithic alumina aerogels, J Non-Cryst Solids (2001); 285(1): 57-63.
CrossRef
- Z.Y. Deng, T. Fukasawa, M. Ando, G.J. Zhang, T. Ohji, High-surface-area alumina ceramics fabricated by the decomposition of Al(OH)3, Journal of the American Ceramic Society 84(3) (2001) 485-491.
CrossRef
- D. Trimm, A. Stanislaus, The control of pore size in alumina catalyst supports: A review, Applied Catalysis 21(2) (1986) 215-238.
CrossRef
- J. Ganley, K. Riechmann, E.G. Seebauer, R. Masel, Porous anodic alumina optimized as a catalyst support for microreactors, Journal of Catalysis 227(1) (2004) 26-32.
CrossRef
- B.-H. Yoon, W.-Y. Choi, H. -E. Kim, J.-H. Kim, Y. -H. Koh, Aligned porous alumina ceramics with high compressive strengths for bone tissue engineering, Scripta Mater 58(7) (2008) 537-540.
CrossRef
- N. Hezil, M. Fellah, Synthesis and structural and mechanical properties of nanobioceramic (α-Al2O3), Journal of the Australian Ceramic Society (2019).
CrossRef
- M. Rahmati, M. Mozafari, Biocompatibility of alumina‐based biomaterials–A review, Journal of cellular physiology 234(4) (2019) 3321-3335.
CrossRef
- K. Nielsch, J. Choi, K. Schwirn, R.B. Wehrspohn, U. Gösele, Self-ordering regimes of porous alumina: the 10 porosity rule, Nano letters 2(7) (2002) 677-680.
CrossRef
- A. Yamaguchi, F. Uejo, T. Yoda, T. Uchida, Y. Tanamura, T. Yamashita, N. Teramae, Self-assembly of a silica–surfactant nanocomposite in a porous alumina membrane, Nat Mater 3(5) (2004) 337.
CrossRef
- W. Lee, R. Ji, U. Gösele, K. Nielsch, Fast fabrication of long-range ordered porous alumina membranes by hard anodization, Nat Mater 5(9) (2006) 741.
CrossRef
- E. Hammel, O. -R. Ighodaro, O. Okoli, Processing and properties of advanced porous ceramics: An application based review, Ceram Int 40(10) (2014) 15351-15370.
CrossRef
- J. Gu, C. Ren, X. Zong, C. Chen, L. Winnubst, Preparation of alumina membranes comprising a thin separation layer and a support with straight open pores for water desalination, Ceram Int 42(10) (2016) 12427-12434.
CrossRef
- H. Fang, J.F. Gao, H.T. Wang, C.S. Chen, Hydrophobic porous alumina hollow fiber for water desalination via membrane distillation process, Journal of Membrane Science 403-404 (2012) 41-46.
CrossRef
- H. Fang, J. Gao, H. Wang, C. Chen, Hydrophobic porous alumina hollow fiber for water desalination via membrane distillation process, Journal of membrane science 403 (2012) 41-46.
CrossRef
- J. Adler, Ceramic diesel particulate filters, Int J Appl Ceram Tec 2(6) (2005) 429-439.
CrossRef
- S. Shingubara, Fabrication of nanomaterials using porous alumina templates, Journal of Nanoparticle Research 5(1-2) (2003) 17-30.
CrossRef
- W. Lee, K. Schwirn, M. Steinhart, E. Pippel, R. Scholz, U. Gösele, Structural engineering of nanoporous anodic aluminium oxide by pulse anodization of aluminium, Nature nanotechnology 3(4) (2008) 234.
CrossRef
- F. Caruso, R.A. Caruso, H. Möhwald, Nanoengineering of inorganic and hybrid hollow spheres by colloidal templating, Science 282(5391) (1998) 1111-1114.
CrossRef
- C.G. Göltner, Porous solids from rigid colloidal templates: morphogenesis, Angewandte Chemie International Edition 38(21) (1999) 3155-3156.
CrossRef
- Y. Sun, Y. Xia, Shape-controlled synthesis of gold and silver nanoparticles, Science 298(5601) (2002) 2176-2179.
CrossRef
- A. Kalemtas, G. Topates, H. Özcoban, H. Mandal, F. Kara, R. Janssen, Mechanical characterization of highly porous β-Si3N4 ceramics fabricated via partial sintering & starch addition, Journal of the European Ceramic Society 33(9) (2013) 1507-1515.
CrossRef
- A. Kalemtas, Low-Temperature Sintering of Porous Ceramics Via Sodium Borate Addition, Material Science Research India 16(1) (2019) 48-55.
CrossRef
- T. Ohji, M. Fukushima, Macro-porous ceramics: processing and properties, International Materials Reviews 57(2) (2012) 115-131.
CrossRef
- S.C. Nanjangud, R. Brezny, D.J. Green, Strength and Young’s modulus behavior of a partially sintered porous alumina, Journal of the American Ceramic Society 78(1) (1995) 266-268.
CrossRef
- J.-F. Yang, G.-J. Zhang, T. Ohji, Porosity and microstructure control of porous ceramics by partial hot pressing, J Mater Res 16(7) (2001) 1916-1918.
CrossRef
- A. Kalemtaş, N. Özey, M.T.A. Aydin, Processing of layered porous mullite ceramics, Journal of the Australian Ceramic Society 54(3) (2018) 545-555.
CrossRef
- X. Liang, Y. Li, L. Pan, S. Sang, T. Zhu, B. Li, C.G. Aneziris, Preparation and enhancement of mullite reticulated porous ceramics for porous media combustion, Ceram Int (2019).
CrossRef
- S. Bose, C. Das, Preparation and characterization of low cost tubular ceramic support membranes using sawdust as a pore-former, Materials Letters 110 (2013) 152-155.
CrossRef
- S. Bose, C. Das, Sawdust: From wood waste to pore-former in the fabrication of ceramic membrane, Ceram Int 41(3) (2015) 4070-4079.
CrossRef
- J. Liu, Y. Li, Y. Li, S. Sang, S. Li, Effects of pore structure on thermal conductivity and strength of alumina porous ceramics using carbon black as pore-forming agent, Ceram Int 42(7) (2016) 8221-8228.
CrossRef
- I. Farahbakhsh, Z. Ahmadi, M.S. Asl, Densification, microstructure and mechanical properties of hot pressed ZrB2–SiC ceramic doped with nano-sized carbon black, Ceram Int 43(11) (2017) 8411-8417.
CrossRef
- J.F. Yang, G.J. Zhang, T. Ohji, Fabrication of low‐shrinkage, porous silicon nitride ceramics by addition of a small amount of carbon, Journal of the American Ceramic Society 84(7) (2001) 1639-1641.
CrossRef
- J.K. Cochran, Ceramic hollow spheres and their applications, Current Opinion in Solid State and Materials Science 3(5) (1998) 474-479.
CrossRef
- E. Bae, S. Chah, J. Yi, Preparation and characterization of ceramic hollow microspheres for heavy metal ion removal in wastewater, Journal of colloid and interface science 230(2) (2000) 367-376.
CrossRef
- T.Y. Klein, L. Treccani, K. Rezwan, Ceramic microbeads as adsorbents for purification technologies with high specific surface area, adjustable pore size, and morphology obtained by ionotropic gelation, Journal of the American Ceramic Society 95(3) (2012) 907-914.
CrossRef
- J. Yu, W. Liu, H. Yu, A one-pot approach to hierarchically nanoporous titania hollow microspheres with high photocatalytic activity, Crystal growth and design 8(3) (2008) 930-934.
CrossRef
- X. Sun, J. Liu, Y. Li, Use of carbonaceous polysaccharide microspheres as templates for fabricating metal oxide hollow spheres, Chemistry–A European Journal 12(7) (2006) 2039-2047.
CrossRef
- S. Wang, J. Zhang, J. Jiang, R. Liu, B. Zhu, M. Xu, Y. Wang, J. Cao, M. Li, Z. Yuan, S. Zhang, W. Huang, S. Wu, Porous ceria hollow microspheres: Synthesis and characterization, Micropor Mesopor Mat 123(1) (2009) 349-353.
CrossRef
- Z. Liu, H. Bai, D. Sun, Facile fabrication of hierarchical porous TiO2 hollow microspheres with high photocatalytic activity for water purification, Applied Catalysis B: Environmental 104(3) (2011) 234-238.
CrossRef
- S.F. Wang, F. Gu, M.K. Lü, Sonochemical synthesis of hollow PbS nanospheres, Langmuir 22(1) (2006) 398-401.
CrossRef
- W. Lai, C. Chen, X. Ren, I.-S. Lee, G. Jiang, X. Kong, Hydrothermal fabrication of porous hollow hydroxyapatite microspheres for a drug delivery system, Materials Science and Engineering: C 62 (2016) 166-172.
CrossRef
- Z. Liu, D.D. Sun, P. Guo, J.O. Leckie, One‐step fabrication and high photocatalytic activity of porous TiO2 hollow aggregates by using a low‐temperature hydrothermal method without templates, Chemistry–A European Journal 13(6) (2007) 1851-1855.
CrossRef
- W.S. Cheow, S. Li, K. Hadinoto, Spray drying formulation of hollow spherical aggregates of silica nanoparticles by experimental design, Chemical Engineering Research and Design 88(5-6) (2010) 673-685.
CrossRef
- P. Roy, G. Bertrand, C. Coddet, Spray drying and sintering of zirconia based hollow powders, Powder Technology 157(1-3) (2005) 20-26.
CrossRef
- K. Kho, K. Hadinoto, Aqueous re-dispersibility characterization of spray-dried hollow spherical silica nano-aggregates, Powder Technology 198(3) (2010) 354-363.
CrossRef
- D.M. Kempaiah, S. Yin, T. Sato, A facile and quick solvothermal synthesis of 3D microflower CeO2 and Gd: CeO2 under subcritical and supercritical conditions for catalytic applications, CrystEngComm 13(3) (2011) 741-746.
CrossRef
- S. Lei, K. Tang, Q. Yang, H. Zheng, Solvothermal Synthesis of Metastable γ‐MnS Hollow Spheres and Control of Their Phase, European journal of inorganic chemistry 2005(20) (2005) 4124-4128.
CrossRef
- M.G. Ma, J.F. Zhu, Solvothermal synthesis and characterization of hierarchically nanostructured hydroxyapatite hollow spheres, European Journal of Inorganic Chemistry 2009(36) (2009) 5522-5526.
- T. Martin, A. Galarneau, F. Di Renzo, F. Fajula, D. Plee, Morphological control of MCM‐41 by pseudomorphic synthesis, Angewandte Chemie International Edition 41(14) (2002) 2590-2592.
CrossRef
- H. Wang, F. Wang, Q. Liao, X. Li, Synthesis of millimeter-scale Al2O3 ceramic hollow spheres by an improved emulsion microencapsulation method, Ceram Int 41(3) (2015) 4959-4965.
CrossRef
- F. Caruso, X. Shi, R.A. Caruso, A. Susha, Hollow titania spheres from layered precursor deposition on sacrificial colloidal core particles, Advanced Materials 13(10) (2001) 740-744.
CrossRef
- L. Zhang, G. Jia, H. You, K. Liu, M. Yang, Y. Song, Y. Zheng, Y. Huang, N. Guo, H. Zhang, Sacrificial template method for fabrication of submicrometer-sized YPO4: Eu3+ hierarchical hollow spheres, Inorganic chemistry 49(7) (2010) 3305-3309.
CrossRef
- H. Li, C.-S. Ha, I. Kim, Facile fabrication of hollow silica and titania microspheres using plasma-treated polystyrene spheres as sacrificial templates, Langmuir 24(19) (2008) 10552-10556.
CrossRef
- K. Richardson, M. Akinc, Preparation of spherical yttrium oxide powders using emulsion evaporation, Ceram Int 13(4) (1987) 253-261.
CrossRef
- P.J. Bruinsma, A.Y. Kim, J. Liu, S. Baskaran, Mesoporous silica synthesized by solvent evaporation: spun fibers and spray-dried hollow spheres, Chemistry of Materials 9(11) (1997) 2507-2512.
CrossRef
- J. Pan, L. Zhong, M. Li, Y. Luo, G. Li, Microwave‐Assisted Solvothermal Synthesis of VO2 Hollow Spheres and Their Conversion into V2O5 Hollow Spheres with Improved Lithium Storage Capability, Chemistry–A European Journal 22(4) (2016) 1461-1466.
CrossRef
- A. Chakraborty, D. Ghosh, Reexamination of the Kaolinite‐to‐Mullite Reaction Series, Journal of the American Ceramic Society 61(3‐4) (1978) 170-173.
CrossRef
- Y.-F. Chen, M.-C. Wang, M.-H. Hon, Phase transformation and growth of mullite in kaolin ceramics, Journal of the European Ceramic Society 24(8) (2004) 2389-2397.
CrossRef
- Y.F. Chen, M.C. Wang, M.H. Hon, Phase transformation and growth of mullite in kaolin ceramics, J Eur Ceram Soc 24(8) (2004) 2389-2397.
CrossRef
- O. Castelein, B. Soulestin, J.P. Bonnet, P. Blanchart, The influence of heating rate on the thermal behaviour and mullite formation from a kaolin raw material, Ceram Int 27(5) (2001) 517-522.
CrossRef
- R. Oyamada, The Mechanism of Mullite Formation in Low-Grade Kaolin at Low-Temperatures, Denki Kagaku 49(5) (1981) 286-292.
- T. Sahraoui, H. Belhouchet, M. Heraiz, N. Brihi, A. Guermat, The effects of mechanical activation on the sintering of mullite produced from kaolin and aluminum powder, Ceram Int 42(10) (2016) 12185-12193.
CrossRef
- M. Fahad, U. Farid, Y. Iqbal, Phase and Microstructural Evolution, and Densification Behaviour of Kaolin Powder Compacts, Trans Indian Ceram S 75(1) (2016) 47-52.
CrossRef
- F. Zibouche, H. Kerrioudj, T.A. Mohamed, Structural Characterization of Mullite Formed from Heated Kaolin of Tamazert deposit (Algeria), Asian J Chem 24(3) (2012) 1118-1124.
- J.E. Zhou, X.Z. Zhang, J. Zhang, Y.Q. Wang, S.K. Zhao, X.E. Cai, Influence of Clay Materials on Acicular Mullite Porous Ceramic, Chinese Ceramics Communications Ii 412 (2012) 344-347.
CrossRef
- H.Y. Wang, C.S. Li, Z.J. Peng, S.J. Zhang, Characterization and thermal behavior of kaolin, J Therm Anal Calorim (2011); 105(1): 157-160.
CrossRef
- S. Agathopoulos, H.R. Fernandes, D. Tulyaganov, J.M.F. Ferreira, Preparation of mullite whiskers from kaolinite using CuSO4 as fluxing agent, Advanced Materials Forum Ii (2004); 455-456: 818-821.
CrossRef
- S. Kawai, M. Yoshida, G. Hashizume, Preparation of Mullite from Kaolin by Dry-Grinding, Nippon Seram Kyo Gak (1990); 98(7): 669-674.
CrossRef
- K. Okada, N. Otsuka, S. Somiya, Review of Mullite Synthesis Routes in Japan, Am Ceram Soc Bull (1991); 70(10): 1633-1640.
- L.A. Perezmaqueda, J.L. Perezrodriguez, G.W. Scheiffele, A. Justo, P.J. Sanchezsoto, Thermal-Analysis of Ground Kaolinite and Pyrophyllite, J Therm Anal Calorim (1993); 39(8-9): 1055-1067.
- A.K. Chakravorty, D.K. Ghosh, Kaolinite Mullite Reaction-Series – the Development and Significance of a Binary Aluminosilicate Phase, Journal of the American Ceramic Society (1991); 74(6): 1401-1406.
CrossRef
- A.K. Chakraborty, Supplementary Alkali Extraction Studies of 980-Degrees-C-Heated Kaolinite by X-Ray-Diffraction Analysis, J Mater Sci (1992); 27(8): 2075-2082.
CrossRef
- A.K. Chakraborty, Resolution of Thermal Peaks of Kaolinite in Thermomechanical Analysis and Differential Thermal-Analysis Studies, Journal of the American Ceramic Society (1992); 75(7): 2013-2016.
CrossRef
- J.A. Pask, A.P. Tomsia, Formation of Mullite from Sol-Gel Mixtures and Kaolinite, Journal of the American Ceramic Society (1991); 74(10): 2367-2373.
CrossRef
- K. Srikrishna, G. Thomas, R. Martinez, M.P. Corral, S. Deaza, J.S. Moya, Kaolinite Mullite Reaction-Series – a Tem Study, J Mater Sci (1990); 25(1b): 607-612.
CrossRef
- A.K. Chakraborty, Phase transformation of kaolinite clay, Springer 2014.
CrossRef

This work is licensed under a Creative Commons Attribution 4.0 International License.