Proton Exchange Membrane Fuel Cell (PEMFC) Durability Factors, Challenges, and Future Perspectives: A Detailed Review
Introduction
In a Hydrogen fuel cell (HFC), Hydrogen and oxygen are fed into the cell, where an electrochemical reaction between anode and cathode is separated by an ion-exchange membrane.1–5Among all the types of fuel cells, proton exchange membrane fuel cell (PEMFC) has become widely accepted for powering electric devices and vehicles. 6–10 The core of the fuel is a sandwich-like structure where on both sides of the proton exchange membrane, there is a catalyst layer and a gas diffusion layer covers the catalyst layer(Figure 1).2,6,11,12 One side of the membrane acts as an anode, and the other side acts as a cathode. This core is the deciding part for fuel cell efficiency and longevity. 13 Here, the reaction process in the cathode is named Oxygen reduction reaction.4,5,7
Normally, oxygen reduction is a slow reaction. To accelerate this reaction mechanism, carbon nanoparticle-based platinum catalyst is widely used for its unique operation.15The optimum platinum distribution is around 100 micrograms with 2-5 nanometer sizes.16,17 Advantages like larger current density, quiet and instant operation, mobile use feasibility make fuel cells very reliable to use.18–25 As an electrochemical reaction in a fuel cell generates electricity, it has wide and multiple-use from household application to power plant level energy demand.26–29 This technology is comparatively far away from conventional fossil fuel-based engines in the region of carbon footprint.30
The membrane electrode assembly is the prime cost-bearing component in a fuel cell which is around 70 percent of the total fuel cell cost.31 In the total cost of the membrane electrode assembly, 91 percent cost is responsible for platinum (Pt) catalyst and membrane materials.20,32The main goal is to reduce the platinum catalyst in the electrode and to improve the recycling process.18,33,34 For vehicle and mobile energy demand, fuel cell-based on proton exchange membrane is an appropriate choice.18,33,35 The required longevity and the cost reduction are the main challenges yet to achieve. 18,20,25,36–38 Longevity investigation for fuel cell systems is costly and time-consuming.Around five years of the continuous fuel cell,the experimental operation is needed to achieve the forty-thousand-hour lifetime level.To make fuel cells feasible for widespread use, there are some challenges.25,36,39,40 Relative to the battery operation,the fuel cell is not durable enough due to the constituent decay.41 The storage technology for hydrogen fuel storage is yet to be cost-effective with proper safety measures.28,42 The storage volume needs to be decreased for hydrogen fuel storage.43,44 Besides, the maintenance cost of a fuel cell is still high apart from the initial building cost.45–47 To make fuel cell relevant in comparison to the other options, these main challenges need to be met.
Cell Durability Factors, Challenges and Solutions
Fuel cell Temperature
Despite the proton exchange membrane’s enormous development, its long-term viability remains an issue. The lifetime of the proton exchange membrane is closely linked to the durability of the catalyst, electrode plate, gas diffusion layer, and gasket.38,48–51 The lifetime of the proton exchange membrane is determined by electrochemical erosion, component erosion, and temperature impact. With the increase in temperature, the proton exchange membrane loses its water and becomes dehydrated. As a consequence, hydrogen gas will reach the cathode side after passing the dehydrated membrane. The bipolar plate, catalyst, and gaskets will be damaged by Hydrogen on the cathode side.
Challenges with Fuel cell Temperature
If the fuel cell continues to run at high temperatures, the proton exchange membrane fuel cell’s durability will deteriorate over time. In a study, a fluid dynamic model with an operating temperature range of 80oCto 120o Cand a pressure range of 0.2 MPa was suggested. 31,52A high- temperature fuel cell performed better in this model, with a higher current density at 80oC rather than 120oC. The anode side’s water production was found to be superior to the cathode side’s. 1Smooth water production was discovered when the temperature was reduced from 120oC to 80 oC. However, it may cause direct damage to the fuel cell, reducing the fuel cell’s durability. 53 A small quantity of water accumulates on the surface of the proton exchange membrane at low temperatures of about 100oC. At high temperatures about 200oC, the sulfonate portion of the Nafion membrane decays, allowing hydrogen gas to flow through the proton exchange membrane and reach the cathode region.1 Temperature effects on Fuel cell durability are shown in Figure 2.
Fuel cell operation at 0 °C or at negative thermal conditions is significant. Water will get iced in the membrane electrode assembly, and the ice creates a volume larger than the same amount of water in liquid form. This extra volume in the assembly will create extra pressure and will result in gas diffusion layer carbon fiber damage, catalyst release, membrane crack, etc. 25,55 After the transformation of ice to water will relax the extra volume pressure in the assembly. This pressure and relax situation have a bad effect on fuel cell constituent components, and the fuel cell performance decays.The produced water from the electrochemical reaction needs to be purged before it becomes ice in low thermal conditions for better performance of the fuel cell. A more tolerant gas diffusion layer and proton exchange membrane will ameliorate fuel cell performance in harsh negative thermal conditions.25
The fuel cell has a certain operating temperature which is different from the ambient temperature of the fuel cell. During the electrochemical reaction, heat is one of the by-products in the fuel cell. Internal mass resistance of the fuel cell also generates some heat. Up to 50 to 70 percent of the total input hydrogen fuel is lost from the fuel cell, and it turns into heat energy. 53,56,57 The fuel cell components will be experienced with thermal expansion with the integrated amount of all the thermal energy. The thermal energy difference throughout the electrochemical reaction process will result from irreversible damage to a fuel cell. The gas diffusion layer loses its conductivity of thermal energy with the increment of the fuel cell temperature.
Solution
The temperature should be maintained optimum based on the table 1.1
Table 1: Effect of Temperature on HFC parameters ( adapted from 1)
Parameters
|
Effect on the parameters1,24,29,48,49,57–60
|
Performance and efficiency
|
Increases with the increase in temperature
|
Humidity
|
Optimum temperature maintains the required humidity
|
Power Production
|
Increases with the increase in temperature
|
Voltage
|
Increases with the increase in temperature
|
Leakage
|
Current Increases with the increase in temperature
|
Catalyst
|
Tolerance Increases with the increase in temperature
|
Mass cross-over
|
Decreases with the increase in temperature
|
Durability
|
Decreases with the increase in temperature
|
Presence of Carbon monoxide
Carbon monoxide is very reactive to the platinum catalyst than hydrogen fuel and results in a deposition of carbon monoxide layer over the active surface of the platinum catalyst. After the carbon monoxide deposition, it very difficult to recover the active surface of the catalyst for the further electrochemical reaction.61 Pure hydrogen fuel fed into the fuel cell recovers the damage of carbon monoxide, but it takes a larger time period relative to the damage time.The damaging effect of carbon monoxide depends on some variables, such as the thermal condition, pressure, and flow parameter of hydrogen fuel.61 For the high amount of carbon monoxide impurity in the hydrogen fuel for a long time operation, the membrane will have exposure to severe damage. However, for the higher thermal condition of the fuel cell, the membrane decay will be less.13
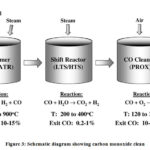 |
Figure 3: Schematic diagram showing carbon monoxide clean up procedure steps in a fuel processor.62
Click here to View figure
|
Challenges with the Presence of Carbon monoxide
The performance of the fuel cell will be decreased regardless of the effect of carbon monoxide is recoverable from pure hydrogen fuel feed.61For a long-term operation of the fuel cell, the carbon monoxide impurity from the hydrogen fuel reacts with the catalyst, which results in catalyst release from the active reaction area.Along the flow channel of the fuel cell, the degradation process happens.63,64The carbon monoxide exposure in the membrane is not uniformly distributed. During the anode half-reaction, the catalyst in the anode side decays.65 Besides, during the cathode half-reaction, the catalyst decay is rapid in the outlet than in the inlet.66 Carbon monoxide has a negative effect on reverse hydrogen movement. This is considered as the contribution to the proton exchange membrane fuel cell durability.67
The operating temperature range for high-temperature proton exchange membrane fuel cells is 100oC to 200oC. 1,68 When the carbondioxide percentage reaches 25 percent and methanol to 10 percent, then the membrane is vulnerable to be affected.69Moist proton exchange membrane is essential for proton exchange from anode to cathode.70 For a certain amount of carbon, dioxide presence creates a negative effect of dilution, which has a negative effect on proton exchange; at a high thermal condition in a high-temperature proton exchange membrane, the reaction mechanism between the carbon monoxide and the catalyst decreases.52 That’s why high-temperature PEMFC operates with better performance compared to the low-temperature PEMFC.
Solution
Major hydrogen fuel generation is obtained from fossil fuel.71 There are different types of impurities that remain during the hydrogen generation process. For the best performance of a fuel cell, the purity of Hydrogen must be 99.999 percent.72 In the hydrogen fuel purification process, carbon monoxide levels must be under ten parts per million. 73,74 Impurity management of hydrogen fuel can be performed in two ways. Either the input hydrogen fuel must be contamination-free, or the tolerance level of the fuel cell be increased.74Adsorbing impurities with the pressure variable is a widely used hydrogen purification process.13 Based on the target impurity elimination, the absorbent material will be changed.Pressure swing adsorption is a mature technology for sizeable industrial-scale purification or gas separation.75 But precise purification process yields less amount of Hydrogen compared to the reformed gas, which is 75 to 90 percent.13,76
Hydrogen purification from membrane separation is cost-effective and takes a comparatively less amount of energy.77Palladium-based membrane surface can capture Hydrogen and forms a metal hydride bond. From the opposite side of the palladium membrane,Hydrogen is released with 99.999% purity.29Hydrogen generation from fossil fuel by steam reforming the carbon monoxide presence rate is very high. This carbon monoxide rate can be reduced from 10 percent to 0.5 percent by the water gas shift reaction method.78This reaction has two thermal conditions.High- temperature reaction mechanisms operate with significant kinetics at temperatures ranging from 350°C to 500°C.76 At low thermal conditions range from 150oCto 250oC, the reaction kinetic is slow but generates a high amount of pure hydrogen fuel because of the equilibrium thermal condition. An introduction of the Platinum cerium-based catalyst during water gas shift reaction shows significant hydrogen fuel purification performance with precise selectivity.78
Extraction of carbon monoxide impurity from hydrogen fuel can be performed with the preferential oxidation method.13,19 With an exposure of oxygen in the reformate gas, this method has the ability to purify hydrogen fuel with the extraction of carbon monoxide from 0.5 percent to 10-part parts per million level.76 This purification method is cost-effective with easy condition maintenance and is suitable for vehicular and stationary or mobile use.42,79A minute amount of oxidant element addition in the reformed hydrogen fuel will minimize the bad effect of impurities on fuel cells.80When air or oxygen is added as an oxidant element, then this process is named air bleeding. If hydrogen peroxide acts as an oxidant element in the membrane and catalyst region, the electrochemical reaction process will be promoted. Air bleeding hydrogen peroxide is also an option to be used as an oxidant element in the fuel cell to prevent the fuel cell membrane corrosion and catalyst layer decay. 78As carbon monoxide is less reactive to the platinum catalyst during high-temperature fuel cells than low temperature. High thermal conditions can enhance the fuel cell tolerance to carbon monoxide impact.67 But during the low-temperature fuel cell, the high thermal condition to protect carbon monoxide effect can be detrimental for the proton exchange membrane because the proton exchange membrane will be damaged in high thermal conditions during the electrochemical reaction process. Humidified proton exchange membrane is significant for the performance and longevity of the fuel cell.51 The water takes the place of the pinhole in the proton exchange membrane and acts as a forbidden zone for carbon monoxide movement from anode to cathode. If oxygen moves through the membrane from cathode to anode, then a low concentration of carbon monoxide will cause significant harm to the proton exchange membrane. This oxygen movement is named oxygen bleeding, which is responsible for the proton exchange membrane decay.39,81The catalyst decay is significant for the fuel, which containsa large percentage of carbon-based impurities.34,39
The input hydrogen purity is essential up to 99.999 % for the reactive and sensitive behavior of the catalyst.72 Normally, CO2, CO, NH3, H2S are the impurities in the fuel cell system.13,81 Hydrogen gas production from the reform method could contain CO up to 0.5 to 10 percent.32,76 For fuel cell operation, CO level should be decreased from the fuel.32 H2S creates a significant amount of damage in the fuel cell system even for a minute amount of presence.82 For NH3,the damage varies according to its trace amount and interval.81 If the trace amount is less, then the damage will be recoverable for a short interval of time. Besides, for the higher trace amount, the damage is irrecoverable for a long interval of time.25Apart from the effect of dilution, methane and nitrogen have no negative effect on the fuel cell.83The presence of formaldehyde (CH2O), acetaldehyde (C2H4O), formic acid (C2H2O), chloromethane (CH3Cl) will cause recoverable damage in a fuel cell.83,84 But a total exposure of all types of impure gases will result in permanent damage tothe proton exchange membrane. 19,46Chloride has an adverse effect on fuel cells. For increased power density during the fuel cell operation, chloride has a negative effect on the fuel cell membrane.13,19 The adverse effect of chloride is related to the amount of chlorine ion which reacts with the platinum catalyst and results in decreasing of the platinum catalyst active area. 13,85
Fuel purification process
For the durability of the fuel cell for vehicle applications, an international organization for standardization (ISO) fixed a level for the percentage of impurities in hydrogen fuel.75 But not all the hydrogen fuel production system meets this level of fuel purification. The water electrolysis hydrogen generation process is far from the ISO fixed production level.86 Carbon emission is high from the water electrolysis hydrogen generation process. The durability, along with the market feasibility of the fuel cell, is yet to be improved.32
The Pressure Swing Adsorption process is a developed method for hydrogen fuel purification within a limited weight and volume.87Hydrogen fuel production from methanol is more feasible for vehicle application. In contrast to hydrogen storage, methanol can be stored in a storage tank with less pressure.Hydrogen fuel production from commercial method contain impurities which are responsible for fuel cell degradation.87 A purity level of hydrogen fuel up to 100 ppm of Carbon monoxide impurity will show better performance along with the catalyst, which is tolerant to Carbon monoxide in low-temperature fuel cells.13
But impurity level over 1000ppm, there must be a purification process for the required purity level of hydrogen fuel before fed into the fuel cell with a precise maintenance method for the durability of the fuel cell, the storage system, storage cylinder, and metal hydride technology yet to be explored and investigated.86 Hydrogen storage material in metal hydride technology is a significant area for pure hydrogen storage and use. In the future, the development of catalyst, electrolyte elements, the membrane will boost the durability of the fuel cell. Middle-temperature proton exchange membrane (PEM) fuel cells in which phosphoric acid is replaced with ionic liquid combine the advantages of low-temperature and high-temperature proton exchange membrane(PEM) fuel cells, showing great potential in the utilization of impure Hydrogen.13, 88
Power supply and transient period
Fuel cell power on and off, high load, etc., are considered transient periods andthese transient periods are responsible for the longevity decay of the fuel cell.89,90 If the fuel cell can operate with a consistent load, the durability of the fuel cell will be higher.91
Challenges regarding Power supply and transient period
During the transition operation, the longevity and the efficiency of the fuel cell decrease. For the interruption of proton flow, there is a polarization difference between the anode to the cathode at a high power load. As a result, fuel cell fails to supply the required energy.39,53 At the beginning of the fuel cell operation, oxygen diffusion occurs, and oxygen reached to anode side from the cathode side. This diffusion process hampers the longevity of the proton exchange membrane fuel cell( Figure 4).89
Solution
The fuel cell shows improved performance and durability for a thin layer of tungsten oxide. This layer will act as an auxiliary catalyst in the fuel cell. It will accelerate to dissociationof Hydrogen and increase the catalyst tolerance level in carbon monoxide.89,92The tungsten oxide has duel conductivity behavior with electron and hydrogen ion conduction in an acidic electrolyte ambiance. For quick response hydrogen capacity, oxygen cleaning during a reaction, energy load sensor, this tungsten-based thin layer is a versatile integration for the durable and efficient fuel cell.89
Humidity and hydration of the fuel cell environment
For better proton exchange through the membrane, hydrogen humidification in fuel cell input is crucial.38,93,94Water maintenance is directly related to the durability and performance of the fuel cell. For a better electrochemical reaction in the fuel cell, the proton exchange membrane needs to be hydrated with optimum conditions.
Challenges regarding Humidity of the fuel cell environment
If the water is not extracted properly, there will be excessive water accumulation in the membrane electrode assembly.31,53,95 With the water flooding, the gas diffusion layer will lose its fuel porosity. So, the input hydrogen gas will not be able to reach the catalyst active reaction area. Finally, the reaction process will be starving with input fuel, and the overall performance and the durability of the fuel cell will be decreased.55,79,96The second half electrochemical reaction is completed on the cathode side, where water is one of the output products. During the proton exchange through the membrane, water molecules also pass through the membrane due to the electro-osmotic process. Total water on the cathode side will also result in water transport from the cathode to the anode side as well. Precise water maintenance in the membrane electrode assembly will ameliorate the overall performance and longevity of the fuel cell. 57The membrane will be damaged due to inconsistent output load and lack of uniformly distributed water.51,92 Besides, a higher level humidification process makes the fuel cell system less easy to handle and becomes costly. The toughest condition for a fuel cell’s durability is the fuel cell starving with hydrogen input fuel.94,97
Solution
To protect fuel cells from the harsh situation, hybrid type cell and a maintaining cell can be introduced under a consistent, stable current density with 0.2 amp/cm-2 where the input gas is changed from Hydrogen to nitrogen gas.89There is a microporous coated layer between the gas diffusion layer and the catalyst layer. This layer is mainly coated in one side of the gas diffusion layer, which is faced in contact with the catalyst layer. Sometimes either side of the gas diffusion layer is coated with a microporous layer. Carbon and hydrophobic element-based microporous layer improve the conductivity of the gas diffusion layer. For optimum humid condition of the gas diffusion layer microporous coating layer is significant.18,50,98A microporous layer is introduced here to make the gas diffusion layer less conductive to the electron. The electron conductivity of the microporous layer is less than the gas diffusion layer. This electron conductivity difference between these two layers increases with the increment of compression value.38,79
Gasket in fuel cell
Silicon, Ethylene Propylene Diene Monomer (EPDM) rubber, andPolytetrafluoroethylene(PTFE) are some of the most widely utilized gasket components for low-temperature-based fuel cells. Gasket materials for higher temperature fuel cells are more challenging to develop since sealing ceramic elements to avoid gas leakage is much more challenging.
Challenges with Gasket in fuel cell
In a long-term fuel cell operation study, traces of silicon-based gasket material were found in the reaction active area.81 The degraded silicon element for gasket decay reaches the catalyst layer on both sides of the proton exchange membrane.This gasket decay process would worsen the sealing pressure, and the cell will suffer from reactant leakage, reactant cross-over, electric short circuit, cooling agent leakage, etc.57During the fuel cell reaction process, the gasket decay element reaches the electrode, which decreases the electrode hydrophobicity and acts as a contaminating agent in the catalyst element.29,81The proton exchange rate of the membrane will be reduced, and the membrane will face mechanical degradation due to the gasket decay process. Consequently, this gasket element will affect the overall performance and durability of the fuel cell. 37,99,100
Solution
Sealing materials ought to have optimal relaxation behavior and processability, enabling for mass manufacturing at a cheap cost and broad fuel cell compatibility.The substances must be free of any possible catalyst poisons that may transfer and damage the proton exchange membrane fuel cell’s (PEMFC) catalyst surface. Furthermore, the materials should not include any elements that may be drained and therefore have the ability to clog openings in the gas-diffusion layer, cover other active areas, or interact in any manner with the cell electrochemistry.57The various temperatures at which the cells are handled, as well as the various media to which the materials must be resistant (water, fuel: H2, O2, reformate, methanol, formic acid, phosphoric acid, coolants), should be considered.48
Catalyst Decay
The platinum (Pt) catalyst is mainly supported by a carbon base which helps to develop inner contact between the catalyst and the proton exchange membrane. With the help of carbon support,the proton is driven to the exchange membrane, and the reaction process accelerates. Any carbon decay will be related to catalyst decay. The catalyst decay means catalyst dissolute or catalyst detach from the catalyst layer. The catalyst release indicates the reduced active reaction area for electrochemical reactions.53Platinum is the most effective catalyst in fuel cell electrochemical reactions. A supporting element and the noble and expensive catalyst will result in a feasible and cost-effective fuel cell operation. 17,34Among the supported elements for catalyst are carbon-based nanotube, graphene, etc. The inclusion of supporting elements along with the catalyst layer boosts fuel cell performance and durability. 55The inverse flow of the cathode and anode may cause dry-wet cyclic stress and degradation of the catalyst layer in the cathode inlet region, according to the surface examination of the catalyst layer (anode outlet area). This causes the catalyst layer to break and the carbon support to corrode. Furthermore, the uncorroded electrolyte will fill in the original microporous structure, reducing the permeability of the catalyst layer and accelerating its mass-transfer efficiency.101
Challenges with catalyst decay
Load variation, lower loading, and the harsh negative thermal condition cause severe damage tothe fuel cell system.18,61,67,73,102Catalyst layer based on Platinum (Pt) and platinum group metal along with carbon or carbon nano-tube has been developed over the recent years which indicate the lower loading of catalyst. 103Due to the high voltage reaction mechanism, the platinum catalyst turns into movable platinum 2+ ion, and the ions become a large collection of ions. Consequently, the active catalyst area will be reduced, and the reaction mechanism in the cathode side will be hampered.102 This collection of platinum ion deposits over the proton exchange membrane and results in the production of membrane degradable radicals of OH. In addition, platinum (Pt2+) ions can also migrate and precipitate in the membrane structure. Thisplatinum (Pt) precipitates can then generate hydroxyl(OH·) radicals, which cause significant membrane degradation.41,60
Solution
To overcome the limitation of the proton exchange membrane, fuel cell due to catalyst and membrane decay membrane with alkaline ion exchange is an appropriate alternative.45,102,104The alkaline membrane is compatible with the non-platinum group catalyst such as transition metal based nitrogen carbon, which will reduce the platinum catalyst loading in the fuel cell and the overall price of the fuel cell will be reduced.105Either with consistent or dynamic power demand, an inappropriate starting condition affects the overall fuel cell performance.If the fuel cell operates with some conditions such as insufficient input hydrogen flow, lack of adequate humid condition, presence of impurities in input gas, then this will be considered as an inappropriate operation condition of a fuel cell.25,106
Water management in the fuel cell
The membrane needs to remain in optimized humid condition for proton exchange from anode to cathode. Water is the output element of the electrochemical reaction in the membrane electrode assembly zone. The extra water is purged from the fuel cell through an external path. Suppose the bad water maintenance in the fuel cell creates an accumulation of excess water. On the cathode side, the oxygen is fed into the fuelcell. Accumulation of excess water will forbid the oxygen to reach the catalyst layer in the cathode electrode. This will result in deceleration of the reaction process in the cathode, and the overall performance of the fuel cell will degrade.39,106This extra water will also responsible for catalyst release from the electrode.31 After the catalyst release, the catalyst will agglomerate and reduce the active reaction area in the electrode. As a result, the thermal condition in the electrode will rise inconsistently, and for the longer operation of the fuel cell, the reaction process will decelerate.53
Membrane Dehydration
Dehydrate membrane is less inclined to exchange proton from anode to cathode. Lack of water content in the membrane electrode region raises potential energy in the anode.51,96 Fuel cell operation with dehydration will affect the chemical structure of the proton exchange membrane. During the hydrated condition, sulfate and ferrous-based impurities are eliminated by the purged water maintenance.However,during the dehydration period, the impurities remain in the membrane electrode region. Hydrogen peroxide is generated in the fuel cell’s electrochemical reaction, and the membrane is very reactive to the hydrogen peroxide and relative elements.34,55 This is a chain reaction mechanism, and all the impurity accumulation erases the membrane wall. As a result, the membrane becomes less strong. Consequently, there will be extra tension compare to the membrane strength, and pinhole-like deformation will generate. Finally, the inconsistent mass cross-over will destroy the proton exchange membrane.53,93,96
Degradation due to the scarcity of reactant gas
The input hydrogen fuel must be purified, and this fuel needs a way to reach the active reaction area. This simple mechanism could be hampered by any cell malfunction or any impurity of input reactant gas.41The carbon-based gas diffusion layer will decay due to reactant insufficiency in the reaction mechanism. 96,107
Effect of impurity in fuel cell
In a membrane electrode assembly is a three-layer arrangement on either side of the proton exchange membrane. The gas diffusion layer, catalyst, proton exchange membrane, catalyst, and gas diffusion layer are the consequential central arrangement of a membrane electrode assembly. This arrangement is attached to each other by hot press technology.19For the required output power demand,many single cells are arranged and attached with nuts and bolts adjustment. This arrangement is called a fuel cell stack. The hot press process and nuts and bolts adjustment impose a compression pressure over the fuel cell system. This compression pressure is significant for the longevity and performance of the fuel cell.
The main functions of the gas diffusion layer in the fuel cell are multipurpose. This layer diffuses input hydrogen fuel uniformly from input flow over the active surface of the catalyst layer. Fuel cells get rid of the extra water with the help of the gas diffusion layer through an external purged channel.57 Electrons from the catalyst layer are driven to an external circuit through the gas diffusion layer.Similarly, the thermal energy produced in the reaction process is transferred to the outer surface to reduce the overall temperature in the membrane electrode assembly.106 The gas diffusion layer is building support in the membrane electrode assembly. This microporous layer eliminates the resistance for hydrogen fuel and required electrical connection during the fuel cell operation. The gas diffusion layer has various types considering the carbon configuration.The gas diffusion layer is also a performance deciding component of the fuel cell during the compressed situation. This layer is a carbon-based layer with a porosity range from 70-85%.37,57Generally, the gas diffusion layer is hydrophobic due to the presence of the polytetrafluoroethylene-based hydrophobic element.91 The gas diffusion layer distributes the input gas uniformly over the active reaction catalyst area and manages the output water during the electrochemical reaction.53,106
Use of Carbon Nanotube
To improve the catalyst response and longevity in the active reaction surface area, the inclusion of supported elements significant.High electron conduction rate, very flimsy with precise hexagonal shape make the carbon nanotube to support catalyst and explore higher active reaction surface area. The addition of carbon nanotube as platinum catalyst support shows higher power density and reaction response and decreases platinum catalyst loading in the fuel cell.108 The platinum catalyst is distributed over the inner and outer walls of the carbon nanotube. This platinum and carbon nanotube combination is propitious for fuel cell electrochemical reactions. For a sustainable catalytic activity with less decay, the inclusion of carbon nanotube is significant. Besides, oxides are not stable in carbon nanotube surfaces.108
Mechanical pressure in fuel cell structure
To build a fuel cell with gas leakage-free, well surface contact among the components, adequate thermal and electric energy release, there is a need fora certain amount of compression. There are external and internal types of compression. Imposed compression at the time of fuel cell building is an external type.
Challenges with Mechanical pressure in fuel cell structure
Excessive external compression will lead to fiber crack or damage, and consequently, the diffusion layer will lose its porosity, and the fuel cross-over resistance will be high. At the same time, the produced water in the core of the fuel cell will be trapped and will create a flooding environment.57 At a compressed value rise from 0 megapascals to 2 MPa, the fuel cell shows performance development. However, for the pressure range over 5 MPa, the fuel cell performance fall rapidly.95
Solution
Mechanical pressure should be maintained in optimum level. The other related factors affecting the pressure should be optimized.The membrane humidification, thermal condition, and the operation cycle also should be controlled to maintain pressure at the core of the membrane electrode assembly.57,98
Membrane composition and structure
Holes, tears, and non-uniform thickness are the mechanical defects in the membrane that mainly occurs due to manufacturing error, membrane electrode assembling process, building pressure or stress, etc.50,109
Challenges with Membrane decay
The input hydrogen and oxygen will pass through the crack or the hole. In this way, the reactant will react will each other through the sudden combustion of Hydrogen and oxygen, which is a safety concern. This reactant pass-through will also create resistance with heat and water maintenance in the membrane electrode assembly. The integrated thermal energy in the membrane electrode assembly has a degrading effect on the proton exchange membrane. The hydrophilic group to the membrane is very prone to be decomposed at high thermal conditions.18,110Membrane thickness is very crucial for fuel cell performance. Thicker membranes are durable in chemical and mechanical stress.51,79 Besides,a thinner membrane is more suitable for proton exchange from the anode side to the cathode side. The membrane also degrades due to the chemical environment. The intermediate radicals of peroxide or hydroperoxide make the membrane to be decomposed during the fuel cell operation.Iron and copper ions form due to electron collector plate decay. This ion act as an accelerating agent for the above-mentioned radical formation, and the aftermath of this action is thinner membrane formation. Fuel cell operation hampers drastically due to the short circuit due to the thin layer of the proton exchange membrane. The catalyst in the cathode side reacts with the input oxygen and form platinumoxides. After that, this platinum oxide generates platinum ions due to the availability of reaction output water. This ion then reaches the proton exchange membrane, and by a reduction reaction process, the platinum ion makes a layer over the membrane. This layer over the membrane decreases the fuel cell performance and durability.
Solution
Proton exchange and durability features during fuel cell operation should be maintained to provide the optimum conditions for proton exchange membrane.111–114Membrane thickness should be optimum to stand with the susceptibility to degradation. The thermal energy should be controlled.
Conclusion
In the future years, hydrogen fuel cells are going to be a viable source of renewable energy. Fuel cells are seen as a promising contender to replace fossil fuel based operation in modern automobiles, as there is an increasing desire to reduce environmental damage caused by burning of fossil fuels. A simple and dependable fuel cell technology is necessary for the deployment of fuel cell-based propulsion. Proton exchange membrane fuel cell is the best choice which has emission-free operation in which oxygen from the environment is used for input reactant oxidant gas and cooling. This process helps to decrease the operation cost of the fuel cell. The main disadvantage of proton exchange membrane fuel cells is the cell performance is highly dependent on the ambient conditions. However, the technology is still not economically viable because of the high operating and maintenance costs. Efficient catalysts for proton exchange membrane fuel cells (PEMFC) will face ever-increasing pressures in terms of cost, activity, durability, and efficiency. Several research examining the performance of the proton exchange membrane fuel cell and various factors impacting it have been undertaken and presented.A larger portion of these costs is related to the durability factors of the fuel cell. To accelerate the widespread adoption of fuel cells, it is critical to extract and discuss key findings from earlier studies, as well as to identify gaps that need to be addressed. In this study, we have presenteda number of factors having a substantial impact, the challenges, and necessary solution. For optimal use and durability, all of these factors should be taken into account. This study provides a complete overview of the current state of the proton exchange membrane fuel cell development and discusses numerous factors that may have an impact on future improvements.
Highlights
Different factors have effects on the durability of the Hydrogen fuel cell.
The effects of different durability factorsforhydrogen fuel cells, challenges and solutions have been discussed.
Acknowledgement
Md
Shehan Habib:
Conceptualization, Writing, Review & Editing
Paroma Arefin: Resources,
Validation, Writing – Original Draft
Md Abdus Salam: Conceptualization,
Writing, Review & Editing, Supervision
Kawsar
Ahmed: Writing – Original Draft
Md.
Sahab Uddin: Literature review, writing original draft
Tareq
Hossain: Literature review, writing
original Draft
Nasrin
Papri: Literature review, writing
original draft
Tauhidul Islam: Literature review, Review & Editing
Conflict of Interest
The authors do not have any conflict of interest.
Funding Source
The author(s) received no financial support for the research, authorship, and/or publication of this article.
References
- Salam, M. A.; Habib, M. S.; Arefin, P.; Ahmed, K.; Uddin, M. S.; Hossain, T.; Papri, N. Effect of Temperature on the Performance Factors and Durability of Proton Exchange Membrane of Hydrogen Fuel Cell: A Narrative Review. Material Science Research India2020, 17 (2), 179–191. https://doi.org/10.13005/msri/170210.
CrossRef - Tanç, B.; Arat, H. T.; Baltacıoğlu, E.; Aydın, K. Overview of the next Quarter Century Vision of Hydrogen Fuel Cell Electric Vehicles. International Journal of Hydrogen Energy2019, 44 (20), 10120–10128. https://doi.org/10.1016/j.ijhydene.2018.10.112.
CrossRef - Kale, S. A Review Paper on Electrical System Consisting of Fuel Cell. 2016, No. November 2015.
CrossRef - Salvi, B. L.; Subramanian, K. A. Sustainable Development of Road Transportation Sector Using Hydrogen Energy System. Renewable and Sustainable Energy Reviews2015, 51, 1132–1155. https://doi.org/10.1016/j.rser.2015.07.030.
CrossRef - Dawood, F.; Anda, M.; Shafiullah, G. M. Hydrogen Production for Energy: An Overview. International Journal of Hydrogen Energy2020, 45 (7), 3847–3869. https://doi.org/10.1016/j.ijhydene.2019.12.059.
CrossRef - Kaya, K.; Hames, Y. Two New Control Strategies: For Hydrogen Fuel Saving and Extend the Life Cycle in the Hydrogen Fuel Cell Vehicles. International Journal of Hydrogen Energy2019, 44 (34), 18967–18980. https://doi.org/10.1016/j.ijhydene.2018.12.111.
CrossRef - Ajanovic, A.; Haas, R. Economic and Environmental Prospects for Battery Electric- and Fuel Cell Vehicles: A Review. Fuel Cells2019, 19 (5), 515–529. https://doi.org/10.1002/fuce.201800171.
CrossRef - Wang, M. Fuel Choices for Fuel-Cell Vehicles: Well-to-Wheels Energy and Emission Impacts. Journal of Power Sources2002, 112 (1), 307–321. https://doi.org/10.1016/S0378-7753(02)00447-0.
CrossRef - Staffell, I.; Scamman, D.; Velazquez Abad, A.; Balcombe, P.; Dodds, P. E.; Ekins, P.; Shah, N.; Ward, K. R. The Role of Hydrogen and Fuel Cells in the Global Energy System. Energy and Environmental Science2019, 12 (2), 463–491. https://doi.org/10.1039/c8ee01157e.
CrossRef - Teng, T.; Zhang, X.; Dong, H.; Xue, Q. A Comprehensive Review of Energy Management Optimization Strategies for Fuel Cell Passenger Vehicle. International Journal of Hydrogen Energy2020, No. xxxx. https://doi.org/10.1016/j.ijhydene.2019.12.202.
CrossRef - Emadi, A.; Williamson, S. S. Fuel Cell Vehicles: Opportunities and Challenges. 2004 IEEE Power Engineering Society General Meeting2004, 2, 1640–1645. https://doi.org/10.1109/pes.2004.1373150.
CrossRef - Gaikwad, S. D.; Ghosh, P. C. Sizing of a Fuel Cell Electric Vehicle: A Pinch Analysis-Based Approach. International Journal of Hydrogen Energy2020, 45 (15), 8985–8993. https://doi.org/10.1016/j.ijhydene.2020.01.116.
CrossRef - Pei, P.; Wang, M.; Chen, D.; Ren, P.; Zhang, L. Key Technologies for Polymer Electrolyte Membrane Fuel Cell Systems Fueled Impure Hydrogen. Progress in Natural Science: Materials International2020, No. August, 1–13. https://doi.org/10.1016/j.pnsc.2020.08.015.
CrossRef - Choe, G.; Kim, J.; Kang, H.; Lee, B.; Lee, W. Proton Exchange Membrane Fuel Cell (PEMFC) Modeling for High Efficiency Fuel Cell Balance of Plant (BOP). In 2007 International Conference on Electrical Machines and Systems (ICEMS),; 2007; pp 271–276.
- Sui, S.; Wang, X.; Zhou, X.; Su, Y.; Riffat, S.; Liu, C. A Comprehensive Review of Pt Electrocatalysts for the Oxygen Reduction Reaction: Nanostructure, Activity, Mechanism and Carbon Support in PEM Fuel Cells. Journal of Materials Chemistry A2017, 5 (5), 1808–1825. https://doi.org/10.1039/C6TA08580F.
CrossRef - Tan, T. L.; Wang, L.-L.; Zhang, J.; Johnson, D. D.; Bai, K. Platinum Nanoparticle During Electrochemical Hydrogen Evolution: Adsorbate Distribution, Active Reaction Species, and Size Effect. ACS Catalysis2015, 5 (4), 2376–2383. https://doi.org/10.1021/cs501840c.
CrossRef - Jeyaraj, M.; Gurunathan, S.; Qasim, M.; Kang, M.-H.; Kim, J.-H. A Comprehensive Review on the Synthesis, Characterization, and Biomedical Application of Platinum Nanoparticles. Nanomaterials2019, 9 (12), 1719. https://doi.org/10.3390/nano9121719.
CrossRef - Hu, X.; Song, K.; Niu, W.; Zhang, T. Powertrain System Durability in Proton Exchange Membrane Fuel Cell Electric Vehicles: A Review. SAE Technical Papers2018, 2018–April, 1–12. https://doi.org/10.4271/2018-01-1303.
CrossRef - Sorrentino, A.; Sundmacher, K.; Vidakovic-Koch, T. Polymer Electrolyte Fuel Cell Degradation Mechanisms and Their Diagnosis by Frequency Response Analysis Methods: A Review. Energies2020, 13 (21), 5825. https://doi.org/10.3390/en13215825.
CrossRef - Dyantyi, N.; Parsons, A.; Sita, C.; Pasupathi, S. PEMFC for Aeronautic Applications: A Review on the Durability Aspects. Open Engineering2017, 7 (1), 287–302. https://doi.org/10.1515/eng-2017-0035.
CrossRef - Ho, Y. S. Some Comments on: Yonoff et Al.’ Research Trends in Proton Exchange Membrane Fuel Cells during 2008–2018: A Bibliometric Analysis’, Heliyon, 2019, 5: E01724. Heliyon2020, 6 (9), 10–13. https://doi.org/10.1016/j.heliyon.2020.e04848.
CrossRef - Sutharssan, T.; Montalvao, D.; Chen, Y. K.; Wang, W. C.; Pisac, C.; Elemara, H. A Review on Prognostics and Health Monitoring of Proton Exchange Membrane Fuel Cell. Renewable and Sustainable Energy Reviews2017, 75, 440–450. https://doi.org/10.1016/j.rser.2016.11.009.
CrossRef - Fedock, J. A. Low Temperature Polymer Electrolyte Fuel Cell Performance Degradation. Physics and Technical Sciences2013, 1 (2), 15. https://doi.org/10.12966/pts.07.02.2013.
CrossRef - Hamrock, S. J.; Yandrasits, M. A. Proton Exchange Membranes for Fuel Cell Applications. Polymer Reviews2006, 46 (3), 219–244. https://doi.org/10.1080/15583720600796474.
CrossRef - Thangavelautham, J. Degradation in PEM Fuel Cells and Mitigation Strategies Using System Design and Control. Proton Exchange Membrane Fuel Cell2018. https://doi.org/10.5772/intechopen.72208.
CrossRef - Ren, X.; Lv, Q.; Liu, L.; Liu, B.; Wang, Y.; Liu, A.; Wu, G. Current Progress of Pt and Pt-Based Electrocatalysts Used for Fuel Cells. Sustainable Energy and Fuels2019, 4 (1), 15–30. https://doi.org/10.1039/c9se00460b.
CrossRef - Chandran, P.; Ghosh, A.; Ramaprabhu, S. High-Performance Platinum-Free Oxygen Reduction Reaction and Hydrogen Oxidation Reaction Catalyst in Polymer Electrolyte Membrane Fuel Cell. Scientific Reports2018, 8 (1), 1–11. https://doi.org/10.1038/s41598-018-22001-9.
CrossRef - Kuroki, T.; Nagasawa, K.; Peters, M.; Leighton, D.; Kurtz, J.; Sakoda, N.; Monde, M.; Takata, Y. Thermodynamic Modeling of Hydrogen Fueling Process from High-Pressure Storage Tank to Vehicle Tank. International Journal of Hydrogen Energy2021, 46 (42), 22004–22017. https://doi.org/10.1016/j.ijhydene.2021.04.037.
CrossRef - Vermaak, L.; Neomagus, H. W. J. P.; Bessarabov, D. G. Hydrogen Separation and Purification from Various Gas Mixtures by Means of Electrochemical Membrane Technology in the Temperature Range 100–160◦c. Membranes2021, 11 (4). https://doi.org/10.3390/membranes11040282.
CrossRef - Duclos, L.; Chattot, R.; Dubau, L.; Thivel, P. X.; Mandil, G.; Laforest, V.; Bolloli, M.; Vincent, R.; Svecova, L. Closing the Loop: Life Cycle Assessment and Optimization of a PEMFC Platinum-Based Catalyst Recycling Process. Green Chemistry2020, 22 (6), 1919–1933. https://doi.org/10.1039/c9gc03630j.
CrossRef - De Bruijn, F. A.; Dam, V. A. T.; Janssen, G. J. M. Review: Durability and Degradation Issues of PEM Fuel Cell Components. Fuel Cells2008, 8 (1), 3–22. https://doi.org/10.1002/fuce.200700053.
CrossRef - Shiva Kumar, S.; Himabindu, V. Hydrogen Production by PEM Water Electrolysis – A Review. Materials Science for Energy Technologies2019, 2 (3), 442–454. https://doi.org/10.1016/j.mset.2019.03.002.
CrossRef - Whiston, M. M.; Azevedo, I. L.; Litster, S.; Whitefoot, K. S.; Samaras, C.; Whitacre, J. F. Expert Assessments of the Cost and Expected Future Performance of Proton Exchange Membrane Fuel Cells for Vehicles. Proceedings of the National Academy of Sciences of the United States of America2019, 116 (11), 4899–4904. https://doi.org/10.1073/pnas.1804221116.
CrossRef - Holton, O. T.; Stevenson, J. W. The Role of Platinum in Proton Exchange Membrane Fuel Cells Evaluation of Platinum’s Unique Properties for Use in Both the Anode and Cathode of a Proton Exchange Membrane Fuel Cell. @BULLETPlatinum Metals Rev2013, 57 (4), 259–271.
CrossRef - Jourdani, M.; Mounir, H.; El Marjani, A. Compilation of Factors Affecting Durability of Proton Exchange Membrane Fuel Cell (PEMFC). Proceedings of 2014 International Renewable and Sustainable Energy Conference, IRSEC 20142014, 542–547. https://doi.org/10.1109/IRSEC.2014.7059906.
CrossRef - Mustain, W. E.; Chatenet, M.; Page, M.; Kim, Y. S. Durability Challenges of Anion Exchange Membrane Fuel Cells. Energy and Environmental Science2020, 13 (9), 2805–2838. https://doi.org/10.1039/d0ee01133a.
CrossRef - Kannan, A.; Li, Q.; Cleemann, L. N.; Jensen, J. O. Acid Distribution and Durability of HT-PEM Fuel Cells with Different Electrode Supports. Fuel Cells2018, 18 (2), 103–112. https://doi.org/10.1002/fuce.201700181.
CrossRef - Wu, D.; Peng, C.; Yin, C.; Tang, H. Review of System Integration and Control of Proton Exchange Membrane Fuel Cells; 2020; Vol. 3. https://doi.org/10.1007/s41918-020-00068-1.
CrossRef - Wang, Y.; Chen, K. S.; Mishler, J.; Cho, S. C.; Adroher, X. C. A Review of Polymer Electrolyte Membrane Fuel Cells: Technology, Applications, and Needs on Fundamental Research. Applied Energy2011, 88 (4), 981–1007. https://doi.org/10.1016/j.apenergy.2010.09.030.
CrossRef - Shahrukh Shamim, K. Sudhakar, Brajesh Choudhary, J. A. A Review on Recent Advances in Proton Exchange Membrane Fuel Cells : Materials , Technology and Applications. Advances in Applied Science Research2015, 6 (March 2016), 89–100.
- Chen, H.; Song, Z.; Zhao, X.; Zhang, T.; Pei, P.; Liang, C. A Review of Durability Test Protocols of the Proton Exchange Membrane Fuel Cells for Vehicle. Applied Energy2018, 224 (November 2017), 289–299. https://doi.org/10.1016/j.apenergy.2018.04.050.
CrossRef - Rivard, E.; Trudeau, M.; Zaghib, K. Hydrogen Storage for Mobility: A Review. Materials2019, 12 (12). https://doi.org/10.3390/ma12121973.
CrossRef - Brooks, K. P.; Sprik, S. J.; Tamburello, D. A.; Thornton, M. J. Design Tool for Estimating Metal Hydride Storage System Characteristics for Light-Duty Hydrogen Fuel Cell Vehicles. International Journal of Hydrogen Energy2020, 45 (46), 24917–24927. https://doi.org/10.1016/j.ijhydene.2020.05.159.
CrossRef - Cho, S. M.; Kim, C.; Kim, K. S.; Kim, D. K. Lightweight Hydrogen Storage Cylinder for Fuel Cell Propulsion Systems to Be Applied in Drones. International Journal of Pressure Vessels and Piping2021, 104428. https://doi.org/10.1016/j.ijpvp.2021.104428.
CrossRef - Ji, Z.; Perez-Page, M.; Chen, J.; Rodriguez, R. G.; Cai, R.; Haigh, S. J.; Holmes, S. M. A Structured Catalyst Support Combining Electrochemically Exfoliated Graphene Oxide and Carbon Black for Enhanced Performance and Durability in Low-Temperature Hydrogen Fuel Cells. Energy2021, 226, 120318. https://doi.org/10.1016/j.energy.2021.120318.
CrossRef - Song, K.; Wang, X.; Li, F.; Sorrentino, M.; Zheng, B. Pontryagin’s Minimum Principle-Based Real-Time Energy Management Strategy for Fuel Cell Hybrid Electric Vehicle Considering Both Fuel Economy and Power Source Durability. Energy2020, 205, 118064. https://doi.org/10.1016/j.energy.2020.118064.
CrossRef - Jahromi, M. M.; Heidary, H. Durability and Economics Investigations on Triple Stack Configuration and Its Power Management Strategy for Fuel Cell Vehicles. International Journal of Hydrogen Energy2021, 46 (7), 5740–5755. https://doi.org/10.1016/j.ijhydene.2020.11.103.
CrossRef - Bieringer, R.; Adler, M.; Geiss, S.; Viol, M. Gaskets: Important Durability Issues. In Polymer Electrolyte Fuel Cell Durability; Springer New York: New York, NY; pp 271–281. https://doi.org/10.1007/978-0-387-85536-3_13.
CrossRef - Borup, R.; Meyers, J.; Pivovar, B.; Kim, Y. S.; Mukundan, R.; Garland, N.; Myers, D.; Wilson, M.; Garzon, F.; Wood, D.; Zelenay, P.; More, K.; Stroh, K.; Zawodzinski, T.; Boncella, X. J.; Mcgrath, J. E.; Inaba, O. M.; Miyatake, K.; Hori, M.; Ota, K.; Ogumi, Z.; Miyata, S.; Nishikata, A.; Siroma, Z.; Uchimoto, Y.; Yasuda, K.; Kimijima, K.; Iwashita, N. Scientific Aspects of Polymer Electrolyte Fuel Cell Durability and Degradation(Chem Rev_2007_107_3904−3951).Pdf. 2007, 3904–3951.
CrossRef - de Frank Bruijn, A.; Janssen, G. J. M. PEM Fuel Cell Materials: Costs, Performance and Durability; 2017. https://doi.org/10.1007/978-1-4939-2493-6_152-3.
CrossRef - Zhang, J. Investigation of CO Tolerance in Proton Exchange Membrane Fuel Cells. Dissertation2004, 1–219.
- Pinar, F. J.; Rastedt, M.; Pilinski, N.; Wagner, P.; Dyck, A. Demonstrating Feasibility of a High Temperature Polymer Electrolyte Membrane Fuel Cell Operation with Natural Gas Reformate Composition. International Journal of Hydrogen Energy2017, 42 (19), 13860–13875. https://doi.org/10.1016/j.ijhydene.2017.03.161.
CrossRef - Zhao, J.; Li, X. A Review of Polymer Electrolyte Membrane Fuel Cell Durability for Vehicular Applications: Degradation Modes and Experimental Techniques. Energy Conversion and Management2019, 199 (August 2019), 112022. https://doi.org/10.1016/j.enconman.2019.112022.
CrossRef - Thangavelautham, J. Degradation in PEM Fuel Cells and Mitigation Strategies Using System Design and Control. In Proton Exchange Membrane Fuel Cell; InTech, 2018. https://doi.org/10.5772/intechopen.72208.
CrossRef - Choudhury, B.; Escobedo, G.; Curtin, D. E.; Banerjee, S. PEM Hydrogen Fuel Cell Durability: A Perspective Review and Recent Advances. Transworld Research Network2008, 37661 (2), 695–23.
- Dillard, D. A.; Guo, S.; Ellis, M. W.; Lesko, J. J.; Dillard, J. G.; Sayre, J.; Vijayendran, B. Seals and Sealants in PEM Fuel Cell Environments: Material, Design, and Durability Challenges. Fuel Cell Science, Engineering and Technology – 20042004, 553–560. https://doi.org/10.1115/fuelcell2004-2520.
CrossRef - Khetabi, E. M.; Bouziane, K.; Zamel, N.; François, X.; Meyer, Y.; Candusso, D. Effects of Mechanical Compression on the Performance of Polymer Electrolyte Fuel Cells and Analysis through In-Situ Characterisation Techniques – A Review. Journal of Power Sources2019, 424, 8–26. https://doi.org/10.1016/j.jpowsour.2019.03.071.
CrossRef - Hinds, G. Performance and Durability of PEM Fuel Cells : A Review. Materials Performance2004, No. September.
- de Bruijn, F. PEMFC Lifetime and Durability – an Overview. 2011.
- Schenk, A.; Cermenek, B.; Hacker, V. Other Polymer Electrolyte Fuel Cells; 2018. https://doi.org/10.1016/B978-0-12-811459-9.00005-0.
CrossRef - Postole, G.; Auroux, A. The Poisoning Level of Pt/C Catalysts Used in PEM Fuel Cells by the Hydrogen Feed Gas Impurities: The Bonding Strength. International Journal of Hydrogen Energy2011, 36 (11), 6817–6825. https://doi.org/10.1016/j.ijhydene.2011.03.018.
CrossRef - Holt, C.; Azad, A.; Swartz, S.; Rao, R. R.; Dutta, P. Carbon Monoxide Sensor for PEM Fuel Cell Systems. Sensors and Actuators B-chemical2002, 87, 414-420.
CrossRef - Chandesris, M.; Guetaz, L.; Schott, P.; Scohy, M.; Escribano, S. Investigation of Degradation Heterogeneities in PEMFC Stack Aged under Reformate Coupling In Situ Diagnosis, Post-Mortem Ex Situ Analyses and Multi-Physic Simulations. Journal of The Electrochemical Society2018, 165 (6), F3290–F3306. https://doi.org/10.1149/2.0321806jes.
CrossRef - Ren, P.; Pei, P.; Li, Y.; Wu, Z.; Chen, D.; Huang, S. Degradation Mechanisms of Proton Exchange Membrane Fuel Cell under Typical Automotive Operating Conditions. Progress in Energy and Combustion Science2020, 80, 100859. https://doi.org/10.1016/j.pecs.2020.100859.
CrossRef - Uddin, S.; Salam, A.; Habib, S.; Ahmed, K.; Hossain, T.; Papri, N. Various Material Development Strategies for Suitable Catalysts of Photo Catalytic Water Splitting to Green Fuel H2:A Critical Review. Material Science Research India2021, 18 (2). https://doi.org/https://bit.ly/3vxgOSe.
- Chattot, R.; Escribano, S. Ageing Studies of a PEM Fuel Cell Stack Developed for Reformate Fuel Operation in ΜCHP Units: Development of an Accelerated Degradation Procedure. International Journal of Hydrogen Energy2015, 40 (15), 5367–5374. https://doi.org/10.1016/j.ijhydene.2015.01.066.
CrossRef - Franco, A. A.; Guinard, M.; Barthe, B.; Lemaire, O. Impact of Carbon Monoxide on PEFC Catalyst Carbon Support Degradation under Current-Cycled Operating Conditions. Electrochimica Acta2009, 54 (22), 5267–5279. https://doi.org/10.1016/j.electacta.2009.04.001.
CrossRef - Ribeirinha, P.; Abdollahzadeh, M.; Sousa, J. M.; Boaventura, M.; Mendes, A. Modelling of a High-Temperature Polymer Electrolyte Membrane Fuel Cell Integrated with a Methanol Steam Reformer Cell. Applied Energy2017, 202, 6–19. https://doi.org/10.1016/j.apenergy.2017.05.120.
CrossRef - Welaya, Y. M. A.; El Gohary, M. M.; Ammar, N. R. A Comparison between Fuel Cells and Other Alternatives for Marine Electric Power Generation. International Journal of Naval Architecture and Ocean Engineering2011, 3 (2), 141–149. https://doi.org/10.2478/IJNAOE-2013-0057.
CrossRef - Wang, H.; Wang, R.; Sui, S.; Sun, T.; Yan, Y.; Du, S. Cathode Design for Proton Exchange Membrane Fuel Cells in Automotive Applications. Automotive Innovation2021, 4 (2), 144–164. https://doi.org/10.1007/s42154-021-00148-y.
CrossRef - Rosen, M. A.; Koohi-Fayegh, S. The Prospects for Hydrogen as an Energy Carrier: An Overview of Hydrogen Energy and Hydrogen Energy Systems. Energy, Ecology and Environment2016, 1 (1), 10–29. https://doi.org/10.1007/s40974-016-0005-z.
CrossRef - Du, Z.; Liu, C.; Zhai, J.; Guo, X.; Xiong, Y.; Su, W.; He, G. A Review of Hydrogen Purification Technologies for Fuel Cell Vehicles. Catalysts2021, 11 (3), 393. https://doi.org/10.3390/catal11030393.
CrossRef - Alihosseinzadeh, A.; Nematollahi, B.; Rezaei, M.; Lay, E. N. CO Methanation over Ni Catalysts Supported on High Surface Area Mesoporous Nanocrystalline γ-Al 2 O 3 for CO Removal in H 2 -Rich Stream. International Journal of Hydrogen Energy2015, 40 (4), 1809–1819. https://doi.org/10.1016/j.ijhydene.2014.11.138.
CrossRef - Nielsen, M.; Alberico, E.; Baumann, W.; Drexler, H.-J.; Junge, H.; Gladiali, S.; Beller, M. Low-Temperature Aqueous-Phase Methanol Dehydrogenation to Hydrogen and Carbon Dioxide. Nature2013, 495 (7439), 85–89. https://doi.org/10.1038/nature11891.
CrossRef - Du, Z.; Liu, C.; Zhai, J.; Guo, X.; Xiong, Y.; Su, W.; He, G. A Review of Hydrogen Purification Technologies for Fuel Cell Vehicles. Catalysts2021, 11 (3), 1–19. https://doi.org/10.3390/catal11030393.
CrossRef - Kalamaras, C. M.; Efstathiou, A. M. Hydrogen Production Technologies: Current State and Future Developments. Conference Papers in Energy2013, 2013, 1–9. https://doi.org/10.1155/2013/690627.
CrossRef - Mores, P. L.; Arias, A. M.; Scenna, N. J.; Caballero, J. A.; Mussati, S. F.; Mussati, M. C. Membrane-Based Processes: Optimization of Hydrogen Separation by Minimization of Power, Membrane Area, and Cost. Processes2018, 6 (11). https://doi.org/10.3390/pr6110221.
CrossRef - Ebrahimi, P.; Kumar, A.; Khraisheh, M. A Review of Recent Advances in Water-Gas Shift Catalysis for Hydrogen Production. Emergent Materials2020, 3 (6), 881–917. https://doi.org/10.1007/s42247-020-00116-y.
CrossRef - Sazali, N.; Salleh, W. N. W.; Jamaludin, A. S.; Razali, M. N. M. New Perspectives on Fuel Cell Technology: A Brief Review. Membranes2020, 10 (5). https://doi.org/10.3390/membranes10050099.
CrossRef - Valdés-López, V. F.; Mason, T.; Shearing, P. R.; Brett, D. J. L. Carbon Monoxide Poisoning and Mitigation Strategies for Polymer Electrolyte Membrane Fuel Cells – A Review. Progress in Energy and Combustion Science2020, 79, 100842. https://doi.org/10.1016/j.pecs. 2020.100842.
CrossRef - Cheng, X.; Shi, Z.; Glass, N.; Zhang, L.; Zhang, J.; Song, D.; Liu, Z. S.; Wang, H.; Shen, J. A Review of PEM Hydrogen Fuel Cell Contamination: Impacts, Mechanisms, and Mitigation. Journal of Power Sources2007, 165 (2), 739–756. https://doi.org/10.1016/j.jpowsour.2006.12.012.
CrossRef - Lopes, T.; Paganin, V. A.; Gonzalez, E. R. The Effects of Hydrogen Sulfide on the Polymer Electrolyte Membrane Fuel Cell Anode Catalyst: H2S-Pt/C Interaction Products. Journal of Power Sources2011, 196 (15), 6256–6263. https://doi.org/10.1016/j.jpowsour.2011.04.017.
CrossRef - Sauder, R. C. <Effect of Anode Purge on Polymer Electrolyte.Pdf>. 2009.
Molter, T. M. 1,2,3 1. 2014.
- Kodama, K.; Nagai, T.; Kuwaki, A.; Jinnouchi, R.; Morimoto, Y. Challenges in Applying Highly Active Pt-Based Nanostructured Catalysts for Oxygen Reduction Reactions to Fuel Cell Vehicles. Nature Nanotechnology2021, 16 (2), 140–147. https://doi.org/10.1038/s41565-020-00824-w.
CrossRef - Beurey, C.; Gozlan, B.; Carré, M.; Bacquart, T.; Morris, A.; Moore, N.; Arrhenius, K.; Meuzelaar, H.; Persijn, S.; Rojo, A.; Murugan, A. Review and Survey of Methods for Analysis of Impurities in Hydrogen for Fuel Cell Vehicles According to ISO 14687:2019. Frontiers in Energy Research2021, 8. https://doi.org/10.3389/fenrg.2020.615149.
CrossRef - Grande, C. A. Advances in Pressure Swing Adsorption for Gas Separation. ISRN Chemical Engineering2012, 2012, 1–13. https://doi.org/10.5402/2012/982934.
CrossRef - Li, Z.; Zheng, Z.; Xu, L.; Lu, X.; Li, Z.; Zheng, Z.; Xu, L.; Lu, X.; Energy, B. M. C. BMC Energy A Review of the Applications of Fuel Cells in Microgrids : Opportunities and Challenges To Cite This Version : BMC Energy A Review of the Applications of Fuel Cells in Microgrids : Opportunities and Challenges. 2020, 0–23.
CrossRef - Shen, G.; Liu, J.; Wu, H. Bin; Xu, P.; Liu, F.; Tongsh, C.; Jiao, K.; Li, J.; Liu, M.; Cai, M.; Lemmon, J. P.; Soloveichik, G.; Li, H.; Zhu, J.; Lu, Y. Multi-Functional Anodes Boost the Transient Power and Durability of Proton Exchange Membrane Fuel Cells. Nature Communications2020, 11 (1). https://doi.org/10.1038/s41467-020-14822-y.
CrossRef - Mayur, M.; Strahl, S.; Husar, A.; Bessler, W. G. A Multi-Timescale Modeling Methodology for PEMFC Performance and Durability in a Virtual Fuel Cell Car. International Journal of Hydrogen Energy2015, 40 (46), 16466–16476. https://doi.org/10.1016/j.ijhydene.2015.09.152.
CrossRef - Dubau, L.; Castanheira, L.; Maillard, F.; Chatenet, M.; Lottin, O.; Maranzana, G.; Dillet, J.; Lamibrac, A.; Perrin, J. C.; Moukheiber, E.; Elkaddouri, A.; De Moor, G.; Bas, C.; Flandin, L.; Caqué, N. A Review of PEM Fuel Cell Durability: Materials Degradation, Local Heterogeneities of Aging and Possible Mitigation Strategies. Wiley Interdisciplinary Reviews: Energy and Environment2014, 3 (6), 540–560. https://doi.org/10.1002/wene.113.
- Wesselmark, M. Electrochemical Reactions in Polymer Electrolyte Fuel
- Phillips, A.; Ulsh, M.; Neyerlin, K. C.; Porter, J.; Bender, G. Impacts of Electrode Coating Irregularities on Polymer Electrolyte Membrane Fuel Cell Lifetime Using Quasi In-Situ Infrared Thermography and Accelerated Stress Testing. International Journal of Hydrogen Energy2018, 43 (12), 6390–6399. https://doi.org/10.1016/j.ijhydene.2018.02.050.
CrossRef - Vichard, L.; Harel, F.; Ravey, A.; Venet, P.; Hissel, D.; Lyon, B.; Lyon, E. C. De; Lyon, I. ScienceDirect Degradation Prediction of PEM Fuel Cell Based on Artificial Intelligence. International Journal of Hydrogen Energy2020, No. xxxx. https://doi.org/10.1016/j.ijhydene.2020.03.209.
CrossRef - Ous, T.; Arcoumanis, C. Effect of Compressive Force on the Performance of a Proton Exchange Membrane Fuel Cell. Proceedings of the Institution of Mechanical Engineers, Part C: Journal of Mechanical Engineering Science2007, 221 (9), 1067–1074. https://doi.org/10.1243/09544062JMES654.
CrossRef - Khattra, N. S.; Hannach, M. El; Wong, K. H.; Lauritzen, M.; Kjeang, E. Estimating the Durability of Polymer Electrolyte Fuel Cell Membranes Using a Fracture Percolation Model. Journal of The Electrochemical Society2020, 167 (1), 013528. https://doi.org/10.1149/2.0282001jes.
CrossRef - Yue, Y. Performance and Durability of High-Temperature Proton Exchange Membrane Fuel Cells Operated on Propane Reformate. 2019.
CrossRef - Y, C.; OL, E.; D, M.; T, S. A Review of Computational Fluid Dynamics Simulations on PEFC Performance. Journal of Applied Mechanical Engineering2016, 05 (06). https://doi.org/10.4172/2168-9873.1000241.
CrossRef - Joghee, P.; Malik, J. N.; Pylypenko, S.; O’Hayre, R. A Review on Direct Methanol Fuel Cells–In the Perspective of Energy and Sustainability. MRS Energy & Sustainability2015, 2 (1), 1–31. https://doi.org/10.1557/mre.2015.4.
CrossRef - Wu, J.; Yuan, X. Z.; Martin, J. J.; Wang, H.; Zhang, J.; Shen, J.; Wu, S.; Merida, W. A Review of PEM Fuel Cell Durability: Degradation Mechanisms and Mitigation Strategies. Journal of Power Sources2008, 184 (1), 104–119. https://doi.org/10.1016/j.jpowsour.2008.06.006.
CrossRef - Hu, Z.; Xu, L.; Li, J.; Wang, Q.; Shao, Y.; Chen, X.; Dai, W.; Ouyang, M. Mechanistic Insight into the Accelerated Decay of Fuel Cells from Catalyst-Layer Structural Failure. Energy Conversion and Management2021, 227, 113568. https://doi.org/10.1016/j.enconman.2020.113568.
CrossRef - Peng, L.; Wei, Z. Catalyst Engineering for Electrochemical Energy Conversion from Water to Water: Water Electrolysis and the Hydrogen Fuel Cell. Engineering2020, 6 (6), 653–679. https://doi.org/10.1016/j.eng.2019.07.028.
CrossRef - Tian, T.; Tang, J.; Chen, Y.; Tan, J.; Li, S.; Pan, M. Study on Accelerated Stress Test for Fuel Cell Lifetime. International Journal of Electrochemical Science2018, 13 (2), 2022–2032. https://doi.org/10.20964/2018.02.69.
CrossRef - Popov, B. N.; Lee, J.-W.; Kriston, A.; Kim, T. Review—Development of Highly Active and Durable Hybrid Compressive Platinum Lattice Catalysts for Polymer Electrolyte Membrane Fuel Cells: Mathematical Modeling and Experimental Work. Journal of The Electrochemical Society2020, 167 (5), 054512. https://doi.org/10.1149/1945-7111/ab6bc6.
CrossRef - Xie, L.; Kirk, D. W. Stability Comparison of Pt and Ni as Base Metal Catalysts in Anion Exchange Membrane Fuel Cells. Journal of The Electrochemical Society2020, 167 (6), 064519. https://doi.org/10.1149/1945-7111/ab8368.
CrossRef - Ji, M.; Wei, Z. A Review of Water Management in Polymer Electrolyte Membrane Fuel Cells. Energies2009, 2 (4), 1057–1106. https://doi.org/10.3390/en20401057.
CrossRef - Kurtz, J.; Sprik, S.; Saur, G.; Onorato, S. Fuel Cell Electric Vehicle Durability and Fuel Cell Performance. 2018, No. March.
CrossRef - Luo, C.; Xie, H.; Wang, Q.; Luo, G.; Liu, C. A Review of the Application and Performance of Carbon Nanotubes in Fuel Cells. Journal of Nanomaterials2015, 2015. https://doi.org/10.1155/2015/560392.
CrossRef - Amamou, A. A.; Kelouwani, S.; Boulon, L.; Agbossou, K. A Comprehensive Review of Solutions and Strategies for Cold Start of Automotive Proton Exchange Membrane Fuel Cells. IEEE Access2016, 4, 4989–5002. https://doi.org/10.1109/ACCESS.2016.2597058.
CrossRef - El-Kharouf, A.; Chandan, A.; Hattenberger, M.; Pollet, B. G. Proton Exchange Membrane Fuel Cell Degradation and Testing: Review. Journal of the Energy Institute2012, 85 (4), 188–200. https://doi.org/10.1179/1743967112Z.00000000036.
CrossRef - Maury, R.; Auclercq, C.; Devilliers, C.; de Huu, M.; Büker, O.; MacDonald, M. Hydrogen Refuelling Station Calibration with a Traceable Gravimetric Standard. Flow Measurement and Instrumentation2020, 74, 101743. https://doi.org/10.1016/j.flowmeasinst.2020.101743.
CrossRef - Sun, H.; He, C.; Yu, X.; Wu, M.; Ling, Y. Optimal Siting and Sizing of Hydrogen Refueling Stations Considering Distributed Hydrogen Production and Cost Reduction for Regional Consumers. International Journal of Energy Research2019, 43 (9), 4184–4200. https://doi.org/10.1002/er.4544.
CrossRef - Rose, P. K.; Neumann, F. Hydrogen Refueling Station Networks for Heavy-Duty Vehicles in Future Power Systems. Transportation Research Part D: Transport and Environment2020, 83, 102358. https://doi.org/10.1016/j.trd.2020.102358.
CrossRef - Frank, E. D.; Elgowainy, A.; Khalid, Y. S.; Peng, J. K.; Reddi, K. Refueling-Station Costs for Metal Hydride Storage Tanks on Board Hydrogen Fuel Cell Vehicles. International Journal of Hydrogen Energy2019, 44 (57), 29849–29861. https://doi.org/10.1016/j.ijhydene219.09.206.
CrossRef

This work is licensed under a Creative Commons Attribution 4.0 International License.