J. Hinojosa-Torres, T. Rangel-Ortiz and J.M Aceves-Hernández
Universidad Nacional Autónoma de México, Facultad de Estudios Superiores Cuautitlán, Carretera Cuautitlán-Teoloyucan km 2.5, Cuautitlán Izcalli, Estado de México, C.P. 54740, México.
Article Publishing History
Article Received on : 25 May 2013
Article Accepted on : 17 Jun 2013
Article Published :
Plagiarism Check: No
Article Metrics
ABSTRACT:
Circular section rods of Zn-22Al-2Cu (weight %) alloy were prepared by rapid solidification (103 K/s); a semi-continuous vertical cast device with mould cooled with water was used. Rods microstructure consisted of two-phase dendritic cells surrounded by lamellar eutectic and, it is found that cell size depends on the growth rate. Starting from an overheated melt at 540°C and a rod growth rate of 0.23 cm sec-1 a fine microstructure is obtained. From X-Ray Diffraction and Energy Dispersive Spectroscopy studies, alternating lamellas of α's and η's phases are conforming the cells and inter dendritic zone. Rod samples were prepared and tested in tension, offset yield strength of 395 MPa, modulus of elasticity of E = 197.5 GPa, tensile strength of 497 MPa and a percentage elongation of 20 to 28 % were measured. These values are higher than those obtained from pieces prepared by permanent mould casting using the same alloy.
KEYWORDS:
Semi-continuous vertical cast; Equi-axed grains; Equi-axed dendrites, Columnar structure; Eutectoid cells; Lamellar eutectic.
Copy the following to cite this article:
Hinojosa-Torres J, Rangel-Ortiz V, Aceves-Hernández J. M. Rapid Solidification of Zn-22Al-2Cu alloy: Microstructure and Strength. Mat.Sci.Res.India;10(1)
|
Copy the following to cite this URL:
Hinojosa-Torres J, Rangel-Ortiz V, Aceves-Hernández J. M. Rapid Solidification of Zn-22Al-2Cu alloy: Microstructure and Strength. Mat.Sci.Res.India;10(1). Available from: http://www.materialsciencejournal.org/?p=286
|
Introduction
The technological development is sustained by the continuous innovation of materials, where the use of these materials will depend on their properties. In metallic materials it has been found that the preparation way, i.e., the process to lead to the solid state the liquid mass determines an entire group of characteristics which promote its application. Nowadays, a great number of solidification processes exists, since the conventional one as the permanent-mould casting until processes producing amorphous solids. In consequence, the importance of the metallurgy resides in the adequate combination of metallic elements and the selected process of consolidation.
Considering the Zn-22Al-2Cu (wt. %) alloy, improvements in the mechanical properties of this alloy can be obtained by using a semi-continuous casting solidification process.1-3 Grain refinement and more homogeneous distribution of the alloy elements (because of the high cooling rate of the melt) are the known causes of such improvements. A laboratory device to study this way of solidification, using Zn-Al based alloys, has been developed. As a result of the experiments, circular rods of the Zn-22Al-2Cu alloy were obtained.4
The aim of this work is to report the microstructure, properties in tension, hardness and fracture studies in Zn-22Al-2Cu alloy bars obtained by the semi-continuous casting process.
Materials and Methods
Circular bars of Zn-22Al-2Cu (wt. %) alloy 30 mm in diameter with a length of 1.5 m were prepared by using the semi-continuous vertical casting process.4 An aluminium mould cooled with circulating water having a cylindrical cavity was used. The melt was poured into the cavity and the solidifying material was mechanically extracted by the inferior part of this cavity. A second cooling stage was needed directly on the leaving rod by using water dew. Table 1 shows the optimal values, experimentally determined, of the cast parameters.
For microscopic examination, small cylinders (diameter 25 mm, height 10 mm) were extracted along the bar. After the mechanical polishing of one cylinder face, the face was etched using solution 1 containing 200 g CrO3, 15 g Na2SO4, 1000 ml water; immediately, the etched face was rinsed with solution 2 containing 200 g CrO3, 1000 ml water; finally, the etched face was washed in water, dipped in alcohol, and dried with clean air.7,8
X-ray diffraction using a wavelength of 1.5406 Å was utilized. The analysed spectrum was in between 35 to 46° (2θ) with a scanning rate of 0.1° min-1. A D-5000 Siemens machine was employed. Punctual elementary analysis was performed with the aid of an EG & G Ortec System 5000 of 15 kV device.
Results
In the surface of the bar, ring protuberances appeared to each 4.5 mm in the solidification direction. These protuberances are commonly called “cold shuts”. The cold shuts are a consequence of premature solidification caused by excessive heat removal by the mould. The first solid layer that is formed between the liquid and the mould is partially re-melted, such a remelts is a consequence of the thermal isolation of this layer when it is separated of the wall of the mould because of “shrinkage”.9 On the other hand, if part of the bar surface exceeds the “solidus” temperature, low melting point metal can either re-melts at the surface or flow through interdendritic channels in the surface resulting in liquation. The semi continuous vertical casting process was performed at two different casting speeds: 0.23 cm/s at TL = 540°C; 0.03 cm/s at TL = 515°C (TL, liquidus temperature).
Hardness measures were carried out in the longitudinal and radial directions on each bar. The obtained values did not show any difference among the directions; however, the mean value of RB = 71 ± 3 corresponds to test bars that were cast at high speed, while, the mean value of RB = 63 ± 10 corresponds to test bars that were cast at low speed. As it will be seen later on, the dispersion in the obtained values are associated to the difference of microstructures, principally.
Tension test were performed at room temperature (17°C). A strain rate of e = 0.1 sec-1 was established. For test bars having fine structure (i.e., cast at high speed) offset yield strength of σ0.2 = 395 MPa, modulus of elasticity of E = 197.5 GPa, tensile strength of σm = 497 MPa and a percent elongation of εr = 20 to 28 % were determined, while,for test bars cast at low speed σ0.2 = 333 MPa, E = 166.5 GPa, σm = 429 MPa and εr = 4 to 10 % were measured.10 The differences in values in both groups of test bars can be attributed to several factors: grain size; grain microstructure; phase transformations; among others. There is evidence that in this alloy, the different phases present are susceptible of modifying its cell parameters under stress. The cellular reaction
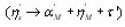
and the four phase transformation

had been observed.11
Low porosity in bars that were cast at high speed was observed. By applying the Arquimedes principle, a density value of 5.41 g/cm3 was determined for this group of test bars. On the contrary, a reduction in the density in bars that were cast to a low speed was observed (4.04 g/cm3). The microscopic examination showed a formation of higher porosity in this last case. The viscosity of the liquid mass at TL = 515°C, limited its flow through the inter-dendritic channels leaving holes in these sites. The average size of the pores was 20 μm for the test bars of high density and 250 to 300 μm for the test bars of low density.
In the cross section of the bars, optical microscopy allowed to observe that bars are conformed by zones with different structure. For the bars cast at high speed, three zones were seen: i) a central zone with an average diameter of 24.8 mm (that it represents 68% of the traverse section); ii) a tin circular ring with a average width of 1.1 mm; iii) an exterior circular ring of a average width of 1.5 mm. The central zone is constituted by equi-axed dendrites of 7.5 μm of average width with an average length of 30 μm (Fig1). This central zone is the last one that solidifies, then, a vigorous convection should cause the breaking of the dendrites and their orientation loss .12 The intermediate ring has a columnar structure radially oriented, which indicates that the heat flow was normal to the wall of the mould. The exterior ring is the first solid formed , equi-axed grains with sizes in between 11 to 75 μm conforms this layer. For the bars cast at low speed, only two zones were seen:i) a central zone with an average diameter of 25.4 mm (that it represents 72.8 % of the traverse section); ii) an exterior circular ring of an average width of 2.3 mm. In this second group of bars, the grain shape in the bar core is made of dendrites in rosette shape (Figure 2) with a rosette diameter of 165 μm and, in the exterior ring, there is an irregular mix of dendrites, pieces of dendrite and equi-axed grains, these last ones with sizes between 15 to 45 μm. Lastly, in the inter-granular zone of the mentioned structures, a two-phase lamellar eutectic was observed (Figure 3). Finally, with the aid of scanning electron microscope, it was found that the dendrites are in fact eutectoid cells (Figure 4) .13 In addition, in detail, the lamellar spacing inside the eutectoid cells is finer than the one observed in the inter-granular zone.
Discussion
As can be seen, the structure evolution of the bars, starting from the wall of mould, can be explained if the “general constitutional super cooling criterion” is taken into account; that is, the liquid immediately in front of the interface is super cooled giving a dendritic structure as a result.
As much the equi-axed grains as the dendrites are conformed by alternated lamellas of α’s and η’s phases, i.e., all grains are eutectoid cells. The α’s phase is an aluminium rich phase, while, the η’s phase is a zinc rich phase (Al-Zn system, according to Presnyakov et al and modified by Goldak and Parr) (Figure 5); both phases are metastable solid solutions. From equilibrium phase diagrams, the zinc is more soluble in the aluminium than the copper, consequently the α’s phase it would be only reinforced by precipitates of zinc.14,15 Then, in the solidification process, the copper would be rejected to the inter-dendritic zone, just as it has been observed.
The increase in the mechanical strength is consequence of the grain refinement and a best distribution of the alloy elements. The ductility of the solids prepared by the semi-continuous vertical cast technique is highest than that obtained by other techniques. This fact is explained by considering that the deformation occurs, principally, through the mechanism of grain boundary sliding before fracture.
Finally, as it is known, the metallic materials have a critical fissure size.16 So, when the material is being deformed, the existent pores grow until reaching the critical size that starts the catastrophic fracture. In the metallic materials the critical fissure size is of the order of tens of micrometers. The bars cast at low speed have pores with sizes in the range of 250 to 300 μm, which means that their pores are closer to the critical size than the pores of the barscast at high speed (20 μm); therefore, the bars cast at high speed will resist bigger deformations without breaking.
Conclusions
By using the semi-continuous vertical cast technique, a lot of bars of Zn-22Al-2Cu alloy were obtained, and, the applied technique produced dendritic structures in the cast material.
A more homogeneous distribution of the alloy elements was attained, avoiding in this way the formation of second phases.
At interior of grains and dendrites a lamellar microstructure conformed by the α’s and η’s phases was observed (eutectoid cells). In the inter-dendritic zone, a two-phase lamellar eutectic was viewed. The lamellas of eutectoid cells are finer than the lamellas of the inter-dendritic eutectic.
Size and shape of grain can be controlled by changing the cast parameters. The mechanical properties such as: offset yield strength; modulus of elasticity; tensile strength; ductility, they were substantially improved.
References
- Emley, E.F.; Int. Met. Rev. (1976); 6(75).
- Brédillon , M.e Kourmani G.; La Fonderia Italiana. (1973); 10(314).
- Evans, J.; Tin and its Uses; (1977); 113(1).
- Hinojosa-Torres, J., Rangel-Ortiz T. y Torres-Villaseñor G.; Título de patente de invención número 172354. Dirección General de Desarrollo Tecnológico, Secretaría de Comercio y Fomento Industrial, MÉXICO.
- Resnick, R. and Halliday D.; Physics, Part I, John Wiley & Sons Inc., New York. (1966); 431.
- Bowman, H. A. and Schoonover, R. M.; Journal of Research (National Bureau of Standards). (1967); 71C(179).
- Rodda, J. L.; Trans. AIME. (1932); 99(149) .
- Rodda, J. L.; Trans. AIME. (1937); 124(189).
- Bergmann, W. J.; Aluminium. (1975); 51(336).
- Hinojosa-Torres, J., Montemayor-Aldrete, J. y, Torres-Villaseñor,G.; Revista Mexicana de Física. (1991); 37(104).
- Hinojosa-Torres J., Cortés-González E., Aceves-Hernández, J. M.,Díaz-del-castillo-Rodríguez, F. and Castaño-Meneses, V. M.; Materials Technology. Advanced Performance Materials. (2012); 27(226).
- Flemings, M. C.; Solidification Processing. McGraw-Hill Book Company, New York. (1974); 224.
- Flemings, M. C.; Solidification Processing. McGraw-Hill Book Company, New York. (1974). 126.
- Torres-Villaseñor, G. and Negrete, J.; “Superplasticity and superplastic Forming”, The Minerals, Metals & Materials Society, C.H. Hamilton and N.E. Paton. (1988); 51.
- Torres-Villaseñor, G. and Van Tendeloo; Phys. Stat. Sol. (A). (1988); 107; 785.
CrossRef
- Dieter, G. E.; Mechanical Metallurgy. McGraw-Hill Kogakusha LTD, Tokyo, Chapter 7. (1976).

This work is licensed under a Creative Commons Attribution 4.0 International License.