Effect of Sintering Temperature on the Properties and Microstructure of A Ceramic Product
R. Vijayaragavan1* and S. Mullainathan2
1Department of Physics, Arasu Engineering College, Kumbakonam, Tamilnadu, India.
2Department of Physics, A.V.C. College of Engineering, Mayiladuthurai, Tamilnadu, India.
DOI : http://dx.doi.org/10.13005/msri/080218
Article Publishing History
Article Received on : 20 Oct 2011
Article Accepted on : 7 Dec 2011
Article Published :
Plagiarism Check: No
Article Metrics
ABSTRACT:
Human activities are always connected with the uses of ceramic materials or ceramic product in every day life. Ceramic materials are typically produced by the application heat upon processed clay and other natural raw materials to form a rigid body. In the present investigation, the mixture of ball Clay, quartz and feldspar are made standard bodies sintered at 900-1050°C and the Ceramic bodies are studied some important properties like, Bulk density, Compressive strength, Porosity, Appearance, Colour and the microstructure analysis of Ceramic bodies using SEM technique.
KEYWORDS:
Ball clay; Quartz; Feldspar; Ceramic bodies; Firing Temperature; SEM; Microstructure
Copy the following to cite this article:
Vijayaragavan R, Mullainathan S. Effect of Sintering Temperature on the Properties and Microstructure of A Ceramic Product. Mat.Sci.Res.India;8(2)
|
Copy the following to cite this URL:
Vijayaragavan R, Mullainathan S. Effect of Sintering Temperature on the Properties and Microstructure of A Ceramic Product. Mat.Sci.Res.India;8(2). Available from: http://www.materialsciencejournal.org/?p=2668
|
Introduction
Clay was one of the earliest materials used to produce ceramics. Two types of clay are generally used which are often termed an china clay and ball clay. Both are Kaolinitic in nature; contain quartz as major impurities mineral along with iron oxide and titania as minor impurities. Ball clays are finer than china clay and often refered to as plastic clay as they provide greater plasticity in a ceramic body.1
Ceramic bodies are normally composed two groups of materials: Plastic and non- plastic material. The plastic material is predominantly based on clays and sometimes kaolin, which are essential to the development of plasticity as well as to reach satisfactory green and dry mechanical strength.2&3 In addition, the plastic material must present favorable rheological properties for an efficient wet milling stage.3&4 Among the non-plastic raw materials, feldspars, talc and quartz are most used. All of them decrease the plasticity, facilitate the defloculation, enhance the packing and increase the permeability of the pieces.4&6 The correct mixture of these (plastic and non-plastic) materials makes the ceramic products able to present the desired technological properties and allows them to be easily processed with the lowest possible cost.2&3 During the firing stage, the feldspars act as a flux supplying alkaline oxide (K2O+Na2O) and also during the sintering stage, the quartz has the function of balancing the ratio between SiO2 and Al2O3 in other to favor the formation of mullite.5 It increases the refractoriness and also increases the expansion coefficient of the body and so decreasing the linear shrinkage.4&6 Quartz, with small particle size in the range of 10-30µm, improves the mechanical strength. By contrast, larger –sized quartz particles tend to decrease the mechanical strength due to susceptibility to micro-crack formation.
Since the microstructure and properties of any ceramic depends on the characteristics of the raw material and processing parameter,7&8 to assure the quality of ceramic products, a complete characterization of the precursor clays as a function of the firing temperature is needed.
Experimental
The raw materials used in this research work are ball clay (50%), Feldspar (25%) and quartz (25%). These mixtures of test specimens (S1, S2, S3, & S4) were prepared by the pressing technique in a (8.0 X 4.5 X 2.5) cm3 rectangular die. After forming, the specimens were dried in open atmosphere (3 days) and then in an oven dried for 24 hours at 110 °C. Then dried samples were fired at 900, 950, 1000 and 1050 °C respectively for 2 hours in a muffle furnace. The important parameters of sintered Ceramic bodies, viz, density, compressive strength, porosity, appearance and colour are determined and the microstructure analysis of Ceramic bodies using SEM (Qunta FEG 200) technique. The bulk density was evaluated by dividing accurately measured mass of sintered samples by external volume (dimensional method9). The Compressive strength was tested using Compressive testing machine. The rate of pressure applied to brick break and break point was measured for compressive strength. The Compressive strength was calculated using the following formula.10 &11
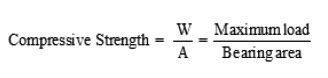
The percentage of Porosity was calculated using the relation.11
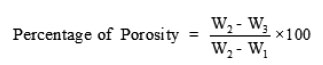
Where by W1 is Weight of the specimen in immersing water. W2 and W3 are Weight of the specimen in air and Weight of the specimen in dried for about six hours to remove the water contents
completely.
Results and Discussion
At least four samples were used for each test and for all categories. The average results are presented and discussed in this section. In the present study, ceramic bodies are analyzed some important properties and microstructure using Scanning electron microscope technique.
Density of Ceramic Bodies
The density affects a number of the properties of the ceramic materials but probably the most important effect is on its strength.11 The measurements of bulk density for mixture of Clay, feldspar and quartz compositions fired at four temperatures 900, 950, 1000, 1050 ºC are demonstrated in figure 1. As shown in figure 1, the bulk density of Ceramic bodies is directly proportional to the firing temperature. This finding closely related to the quantity of water absorbed. When bodies absorb more water, it exhibits a large pore size, resulting is a lighter density.10 &12 The firing temperature can also affect the bulk density of the materials.12 The results show that increasing the temperature results in an increase in bulk density.
Figure 1: Effect of firing temperature on Density of the samples
Compressive Strength Of Ceramic Bodies
Compressive strength test is very important in view of mechanical behaviour measurement technique for ceramic production13 and the compressing test is the most important test for assuring the engineering quality of ceramic/ building materials.10 & 12 The results of the Compressive strength test on the ceramic bodies made from Clay, feldspar and quartz mixtures. The results indicate that the strength is greatly dependent on the firing temperature. The Compressive strength results are shown in figure 2. The results indicated that the firing temperature at which maximum Compressive strength occurred was 1050 °C.
Figure 2: Effect of firing temperature on Compressive strength and porosity of the samples
Porosity of Ceramic Bodies
Porosity is the dominant factor affecting the performance of ceramic material.14 Water absorption is common method of determining the porosity of ceramic bodies. Porosity affects the strength of the materials. Porous bodies are mechanically weak. Lower porosity gives greater strength.15 -16 The measurement of the porosity is used to identify the quality of Ceramic material. In the present investigation, the percentage of porosity value of Ceramic bodies generally lies in the range between 32.20% and 20.15 % (Fig. 2). The higher porosity value is indicating that presence of large void space. From the results, sample S4 (Firing Temperature 1050 °C) having the low porosity has produced high mechanical strength.
Appearance and Colour of Eramic Bodies
Drying is the most important stage of the ceramic manufacturing process. Small cracks may develop during drying, causing a failure during firing17. The firing colour is an also important criterion for the classification of a clay bearing material. The chemical and mineralogical compositions of the ceramic raw materials affect the firing colour to a certain extent.18 In the present study, after drying the samples, no defects were observed. Cracks, bloating and other noticeable defects were not observed after firing. The colour of ceramic bodies was changed from whitish (before firing) to reddish (after firing). After firing, all the samples presented the characteristic homogenous ceramic colour, indicating the uniformity of firing. Appearance and colours of ceramic bodies were acceptable.
Microstructure Analysis of Ceramic Bodies
Figure 3 show the microstructure of the Ceramic bodies sintered at various temperatures. SEM micrographs, taken at increasing firing temperature show the typical sequence of enhanced densification with increasing temperature, characteristics of all studied formulations in this work.
As can be observed, the higher porosity connected with dense zones is clearly visible at 900 °C (figure 3. a) and 950 °C (figure 3. b). At 1000 °C (figure 3.c), the porosity starts to reduce. At 1050 °C (figure 3.d), the Ceramic bodies presented advances sintering stage, in which appearance of nearly spherical isolated pores can be observed. In this state, the open porosity has been reduced.
Figure 3: SEM micrographs of the sintered Ceramic bodies
Conclusion
Based on the results of the present studies, following conclusions can be drawn:
In order to yield a good quality Ceramic product, the mixture of compositions and firing temperature are important key factor. The bulk density of ceramic bricks is directly proportional to the firing temperature.
Compressive strength increases almost linearly with the firing temperature.
The percentage of porosity is inversely proportional to firing temperature. Increase the firing temperature results in decrease in the percentage of Porosity.
Appearance of ceramic bodies is good (no defect) and colours of ceramic bodies were acceptable in all samples.
The microstructure is characterized by a high porosity resulting from the sample S1, sintered at 900 °C.
It is concluded from the work that the composition to produce a good quality of Ceramic bodies was dependent on the maximum firing temperature (1050 °C).
References
- Swapan Kr Das, Kausik Dana, Nar Singh and Ritwik Sarkar, Applied Clay Science 29: 137-143(2005).
CrossRef
- Minichelli, D, De Petris, A, and Ricciardiello, F, Interbrick, 4(6): 17-22(1988).
- Vieira CMF, Da Silva PRN, Da Silva FT, Capitanco JL, and Monteiro SN., Revista Materia, 10(4): 526-536(2005).
- Barba A, Beltran V, Feliu C, Garcia J, Gines F, Sanchez E, and Sanz V, Materias primas para la fabricacion de soportes de baldosas Ceramicas, Instituto de Technologia Ceramica – AICE, Castellon ,291(1997).
- Biffi G, Porcelain stoneware- Production manual and methods of use, Gruppo Editoriale Faenza Editrice S.P.A., Faenza, 304(1999).
- Vieira C.M.F., Pecanha L.A, Jr., and Monteiro S.N., Ceramica, 52: 138-145 (2006).
CrossRef
- Vieira C.M.F., Sanchez R, and Monteiro S.N., Construction and Building Materials, 22: 781-787 (2008).
CrossRef
- Kingery WD, Bowen HK, Uhlmann DR. Introduction to Ceramics, New York: John Wiley & Sons (1976).
- Monteriro, S.N., Pecanha, L.A. and Vieira, C.M.F., Journal of the European Ceramic Soc. 24(8): 2349-2356 (2004).
CrossRef
- Vijayaragavan R and Mullainathan S, Material Science Research India, 8(1): 143-147 (2011)
CrossRef
- Vijayaragavan, R., Janikiraman, G., Satheeskumar, M., Balachandramohan, M., Viruthagiri, B. and Rajamannan. B., Acta Ciencia Indica, XXXIVP, No-1: 023 (2008).
- Deng-Fong Lin and Chih-Huang Weng, journal of Environmental Engineering, 127(10): 922-927 (2001).
- Cem Gol, Production of Ceramic tiles by using Marine Sludge Additives, Master of Science thesis in Chemical Engineering, Izmir Institute of Technology, IZMIR (2006).
- Vasilyeva E.A, Morozova LV, Lapshin A.E, and Kanakov VG, “ceramic materials with controlled porosity”, Journal of Materials physic mechanical, 5: 43-48(2002).
- Sonjida Mustafi, Mainul Ahsan and Dewan, A.H, Bangladesh Journal of Scientific and industrial research, 43(4): 537-544 (2008).
- Evans, A.G., J. of the Am.Ceram.Soc, 73: 187-206 (1990).
CrossRef
- Ismail Demir, Waste Management, 28: 622-627 (2008).
CrossRef
- Oliveira G.E. and Holanda J.N.F. ‘Construction and Building Materials, 18: 437-443 (2004).

This work is licensed under a Creative Commons Attribution 4.0 International License.