Morphology and Corrosion Study of Electroless Ni-P Coatings on Commercial Aluminium Alloy
Rajendra Kumar Duchaniya1, Ashok Sharma1, Manohar Totlani2 and Sushant Upadhyaya3
1Department of Metallurgical and Materials Engineering, Malaviya National Institute of Technology, Jaipur, India.
2Rtd. Head, Surface Engineering BARC, Mumbai, India.
3Department of Chemical Engineering, Malaviya National Institute of Technology, Jaipur, India.
DOI : http://dx.doi.org/10.13005/msri/080215
Article Publishing History
Article Received on : 03 May 2011
Article Accepted on : 17 Jun 2011
Article Published :
Plagiarism Check: No
Article Metrics
ABSTRACT:
The scanning electron microstructure, micro-hardness and conventional corrosion behavior of Electroless Nickel-Phosphorus (E-Ni-P) alloy plating on commercial aluminum substrate in an acidic bath with sodium hypo-phosphite as reducing agent were investigated. Firstly, the scanning electron microscope (SEM) was performed over the coating, the obtained structure resembled as nodular structure. Secondly, Knoop hardness test on coating implies that micro-hardness of nickel–phosphorus coating decrease as bath loading increases. Lastly, corrosion resistant of the nickel-phosphorus coating was evaluated by conventional weight loss method which indicated that the Electroless nickel-phosphorus plating improve the corrosion resistant of commercial aluminum alloy.
KEYWORDS:
Electroless Nickel-Phosphorus; Corrosion; Micro-hardness
Copy the following to cite this article:
Duchaniya R. K, Sharma A, Totlani M, Upadhyaya S. Morphology and Corrosion Study of Electroless Ni-P Coatings on Commercial Aluminium Alloy. Mat.Sci.Res.India;8(2)
|
Copy the following to cite this URL:
Duchaniya R. K, Sharma A, Totlani M, Upadhyaya S. Morphology and Corrosion Study of Electroless Ni-P Coatings on Commercial Aluminium Alloy. Mat.Sci.Res.India;8(2). Available from: http://www.materialsciencejournal.org/?p=2660
|
Introduction
The term “electroless process” is used to describe methods of plating by means of chemical reduction, that is to say, electroless nickel is produced by reducing nickel ions from solutions which contain phosphate, boron, hydrazine compounds.1 Electroless plating differs in one significant respect from all other chemical plating procedures in that it is the only chemical plating process which does not depend on the presence of a couple between galvanically dissimilar metals.
Alloys of nickel and phosphorous are obtained with phosphate ions. The phosphorous content can be varied, normally between 2 and 12 percent, to control strength, ductility, stress, magnetic properties and structure.2 High phosphorous contents obtained in the solutions with a low pH and a high ratio of phosphate to nickel ions favor high strength and low stress. The alloys are supersaturated solid solutions of nickel phosphate in nickel.
There are three main types of Electroless nickel coating3
Nickel phosphorus alloy deposit is generally used for engineering applications. The phosphorus used for engineering content of the alloy deposit varies from 1 to 15 percent and the reducing agent used in the bath is sodium hypophosphite.
Nickel boron alloy deposit is very often used in electroless application for specific deposit characteristics .It is also sometimes used in industrial wear application for its as plated higher hardness than that of nickel phosphorus alloy. The boron content of the alloy can be varied from 0.1 to 10 present. The reducing agent used is diethyl amine borne or sodium boron hydride depending upon the desired alloy composition.
Poly-alloy is a combination of nickel boron or phosphorus and cobalt, iron, tungsten, molybdenum, etc
The most widely used electroless nickel is deposited by the catalytic reduction nickel ions with sodium hypophosphite in acid bath at pH 4.5 to 5 and temperature 85 to 95°c .The deposit contents typically 3 to 12 percent phosphorus by weight.4 The alloy obtained is dependent upon the chemistry of the solution and the operating condition & the phosphorus content significantly influence its chemical and physical properties not only in the as plated condition but also after heat treatment.
The melting temperature is dependent upon the phosphorus content, higher the phosphorus content lowers the melting temperature. The melting temperature of pure nickel is 1450°C whereas for electroless nickel with 7 to 9 phosphorus it is 880°C. In practice this property can be beneficially employed to obtain a desired melting temperature by controlling the phosphorus content of the alloy.
Electroless Nickel-Phosphorus (E-Ni-P) Coating
Electroless nickel plating5 consists of the deposition of a nickel-phosphorous alloy onto the metal surface by a chemical bath, not by electrodes or external electrical charges. An electroless nickel coating is a dense alloy of nickel and phosphorous.6 It is an autocatalytic coating, which simply means it will deposit form solution on certain substrates without any external source of electricity. There are three kinds of E-Ni-P shown in figure (1) based on percentage of phosphorus present in it. Different types have been developed to provide special properties, depending on the end-us requirement.
Figure 1: Types of E-Ni-P
Electroless nickel plating can be used in the as-deposited condition or may be hardened, depending on the intended service conditions. Adhesion of electroless nickel plating to the base metal depends on the ability of the metal to react with the plating solution to form a strong bond. Hardening type stainless steel and alloy steels can be electroless nickel-plated with excellent bonding.7 These materials can be heat treated at 440°C after plating for additional hardness but with lower corrosion resistance. The heat treatment causes diffusion to occur between the atoms of the coating and the substrate. Heating and cooling should be slow to avoid micro cracking due to the difference in the thermal expansion coefficient.
Aluminum can also be electroless nickel-plated with excellent bonding. A surface reaction, such as electroless nickel deposition, can be divided into the following elementary steps:
Diffusion of reactants (Ni++, H2PO) to the surface;
Adsorption of reactants at the surface;
Chemical reaction on the surface;
Desorption of products (HPO—. HI, H+) from the surface;
Diffusion of products away from the surface.
Following mechanism are involved in electroless coating8:
Electrochemical mechanism, where catalytic oxidation of the hypophosphite yield electrons at the catalytic surface which in turn reduces nickel and hydrogen ions is illustrated below:
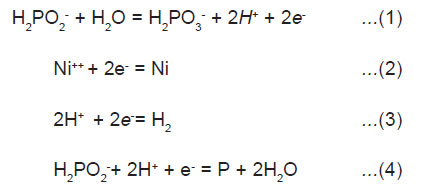
Atomic hydrogen mechanism, where atomic hydrogen is released as the result of the catalytic dehydrogenation of hypophosphite molecule adsorbed at the surface is illustrated below.
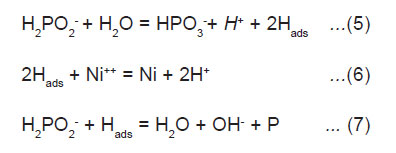
The adsorbed active hydrogen, (6) then reduces nickel at the surface of the catalyst.

Most of the hypophosphite present is catalytic, which is oxidized to orthophosphate and gaseous hydrogen, causing low efficiency of electroless nickel solutions for alloy coating while the deposition of nickel and phosphorus continues.9 The coefficient of utilization of hypophosphite vary a little with the nature of buffer additive; the highest degree of utilization of the hypophosphite was observed in the solution containing sodium acetate, the lowest is that with sodium citrate.10 The main characteristic of the process is the change in the composition of the solution. The concentration of nickel salt and hypophosphite is decreased and the concentration of acid is increased during the progress of deposition.
Following parameter affects the coating process11
Bath content’s concentration
Temperature of bath
pH of solution
Coating time
The surface area of the substrate
Variation in nickel salt concentration has no noticeable influence on the rate of reduction of nickel but variation in hypophosphite concentration affects the process considerably.12 Although increase in hypophosphite concentrations improves the rate of reduction of nickel, extra amounts of reducing agents should not be used as this may cause reduction to take place in the bulk of the solution. The appropriate amount of hypophosphite can be adjusted by observing the bath condition during the course of reaction. Weak hydrogen evolution is an indication of a low concentration of hypophosphite and a vigorous hydrogen evolution indicates excess hypophosphite.13
The concentration of nickel salts has slight influence on the rate of decomposition. Large concentration of nickel salts cause deterioration in the quality of the coatings with the formation of rough deposits. Temperature has a considerable influence on the rate of process. The rate of the process increases with increase in temperature and attains a maximum at about 92 0C. Beyond this temperature, it becomes difficult to maintain the pH of the solution and therefore, the quality of the coating deteriorates.12
Experimental
In the present investigation, commercial aluminum alloy were used as a substrate for EN coating at following bath composition and operating conditions. The experimental set-up is shown in figure(2)
Figure 2: Experimental set-up
Operating conditions maintained in acidic medium bath of above composition are:
Surface Pretreatment
The specimens are cleaned by a series of cleaning chemicals such as bases and acids to have good adhesion. Each chemical pre-treatment is followed by water rinsing to remove the chemical that adheres to the surface. Degreasing removes oil from surface and acid cleaning removes scaling. Activation is done with a weak acid etch, or nickel strike. After the coating process, coated material is finished with an anti-oxidation or anti-tarnish chemical. The flow sheet showing pretreatment process is shown in Figure (3). The steps involved are as follows:
Figure 3: Flowchart of pretreatment steps
Procedure for Electroless Plating
The electroless Ni-P coatings were prepared using an acidic hypophosphite reduced electroless nickel plating bath. Nickel sulphate was the source of nickel while sodium hypophosphite served as the reducing agent then the source of phosphorus. Besides these, the bath also contains suitable amount of complexing agents’ viz. lactic acid and propionic acid Buffering agent NaOH, energy and stabilizers Pb. During plating, the temperature of the bath was maintained at 90oC using a constant temperature water bath and the pH was maintained between 4 and 6 with frequent addition of small quantities of NaOH. The plating solution was mechanically agitated using a hot plate/ magnetic stirrer and Teflon coated magnetic tablet.
Results and Discussion
Electroless Deposited Ni-P Coating
Aluminum is known to be a difficult to plate metal wing to the presence of oxide film resulting in poor adhesion of the coated metal14. Even if the coating is applied after malicious surface di-oxidation minute pores/discontinuities in plating can accelerate corrosion, since aluminum with a standard potential of 1.53 volts is anodic to most of the depositing metals such as Zn, Cu and Ni. An electroless process is known to produce a pore free coating at lower thicknesses than that of electroplating. Besides, electroless baths posses a 100 % throwing power, which ensures uniform plating of small diameter tubes, threaded parts, tanks and large vessels.
The specimen in which the corrosion has not taken place is seen to be of shining nature. This coating is also coherent. This coherent nature is found from the visual, SEM, micro-hardness and Corrosion study by observations
Visual Studies
It is visually observed that coating is adherent and shining in nature. The reasons being defective coating may be as follows:
Surface of aluminum substrate is not properly cleaned and activated.
Not effective control of parameters e.g. temperature and pH. If proper temperature is not attained then coating is not adhered to activated sites of substrate. pH in the process of coating is very much disturbing due to evolution of hydrogen gas.15
Improper stirring, bath should be stirred gently during coating. By doing so coating deposits uniformly on the substrate.
Scanning Electron Microscopy (SEM)
The SEM micrographs of as coated samples of Ni-P were taken at 1.5k, 3.5k, 4.0k magnification. Etching was not done of Al substrate that is why, there are not any grains or grain boundaries observed.
A closer analysis of the coating was observed under SEM. From SEM micrographs Figures (4,5,6). It was observed that the Ni-P film is deposited in the form of spherical globules. The globules have tendency to adhere with the clean upper surface of the substrate. At first, globule is formed on the film at the random places on the substrate. Then these globules grow in the lateral directions on the aluminum substrate. As the first layer is completed after the growth of the globules, the formation of the second layer of the globules started depositing over the previously deposited globules.16 By this continuous process of deposition of globules a coherent film on the substrate developed. This film is quite adherent to the surface of the substrate. Thus, growth of the globules in lateral and vertical direction was noted.
During the deposition of Ni-P electroless coating, the growth starts at isolated nuclei of deposit on the substrate. The whole substrate is then covered by lateral growth of the colonies plugging the discontinuities.
Figure 4: Ni-P Coating at 1500X
Figure 5: Ni-P Coating at 3500X
Figure 6: Ni-P Coating at 4000X
Micro Hardness
The experimental data in table (1) indicated that the micro-hardness decrease with increase in volume of bath. The micro-hardness versus volume of batch relation has shown in figure (7)
Table 1: Variation between volume and micro-hardness
Figure 7: Micro hardness in VH (Y-axis) and volume of bath in ml (X- axis)
Conventional Corrosion Test (Weight Loss Method)
When the plating is put inside the corrosive solution, a galvanic cell is developed and the potential difference is created between the surfaces of the coating and the inner matrix.17 The surface of the coating becomes anodes while the inner matrix of the coating becomes cathode and in this cells a small current flow between these and the surface of the plating starts disintegrating.
Corrosion Rate in Mils Per Year =KW/DAT
Where, T=time of exposure in hours to the nearest 0.01 cm2 ,A=area of the test specimens in cm to the nearest 0.01cm2 ,W=with loss in gms to the nearest 1 mg and D=density of test specimens in gm/cm3. Many different units are used to express corrosion rates. using the above units for A, T ,D and W, the corrosion rate can be calculated in a variety of units whit appropriate value of K. but corrosion rates are usually expressed in mils per year as mpy values usually whole numbers and easy to calculate on a slide rule is used in the present work throughout.
Figure 8: Corrosion rate (in mpy) on y-axis and time (in days) on x-axis of Ni-P coated Al
Conclusion
The following findings resulted from the present investigation:
A uniform film of nickel phosphorous on aluminum substrate has been obtained.
Phosphorous, present in the form of spherical globules, increases corrosion resistance.
The corrosion rates for 3.5% NaCl solution remain linear with a specified time.
Micro hardness increases as the volume of bath increases as bath loading increases.
References
- K.Prker, “Recent Advances in Electroless Nickel Deposits. 8th interfinish Conference,” 1972
- (Basel) G.G. Gawrrilov, Chemical (Electroless) Nickel Plating. Portcullis press. England.1979.
- G.Gutzeit, An Outline of the Chemistry Involved In the process of catalytic Nickel Deposition from Aqueous Solution, Plat. Surf. Finish, 46(10): 1158 (1959).
- A. Brenner and G. Riddell. Deposition of Nickel and Cobalt by Chemical Reduction, J. Res. Natl. Bur. Stand, 39(11): p385 (1947).
- G.O.Mallory, The Electroless Nickel Plating Bath, Electroless Nickel Conference, Cincinnati, Nov 1979.
- Glenn o. Mallory and Juan b. Hajdu ,Electroless Plating: Fundamental And Application, American Electroplater and Surface Finishers Society, Florida 269-270
- J.N Balaraj T.S.N. Sankara Narayana and S.K Seshardi,Elelctroless Ni-P Composit coating, journal of Application Electrochemistry 33:2003,1242
- Elecroless nickel Plating: A Guide, Autistics Plating Company, Inc; Milwaukee, WI 53212.
- R.C Agarwal and Vijaya Agarwal, Electroless alloy/comosit coating: A review, Sadhana Vol. 28, parts 3 & 4, june/augest 2003, 475-493
- Lioyd Plooof ,Elelcroless Nickel Composition Coating ,Adavanced Material & Processess, May 2008, 36-38
- N.Bahiya Baba, W. Waugh, A. M. Davision: Manufacturer of Elelcroless Nickle/YSZ Composit Coting, World Academy of Science, Engineering and Technology 49: 715-720 (2009)
- Electroless Nickle Plating: A General Description of Electorless Nickle Plating and Its Effect on BALTM Seal Perfomence in Reciprocating and Rotary service, Technical Report, Bal Seal Engineering.
- ASM Handbook, Volume 5, Surface Engineering, 290 -309 (1994).
- Glenn o. Mallory and Juan b. Hajdu ,Electroless Plating: Fundamental And Application, American Electroplater and Surface Finishers Society, Florida, 207 -226
- Glenn o. Mallory and Juan b. Hajdu ,Electroless Plating: Fundamental And Application, American Electroplater and Surface Finishers Society, Florida, 107 – 109.
- Glenn o. Mallory and Juan b. Hajdu ,Electroless Plating: Fundamental And Application, American Electroplater and Surface Finishers Society, Florida, 111- 112.
- Glenn o. Mallory and Juan b. Hajdu ,Electroless Plating: Fundamental And Application, American Electroplater and Surface Finishers Society, Florida, 101.

This work is licensed under a Creative Commons Attribution 4.0 International License.