Surface Modification of Acetate Fabric with Water Glass and Silane Compounds for Hydrophobicity
Mohammad Mirjalili
Department of Textile Engineering, Yazd Branch, Islamic Azad University, Yazd, Iran.
DOI : http://dx.doi.org/10.13005/msri/090102
Article Publishing History
Article Received on : 01 Jan 2012
Article Accepted on : 03 Feb 2012
Article Published :
Plagiarism Check: Yes
Article Metrics
ABSTRACT:
Acetate fabric surface was treated with combinations of water glass and hexadecyltrimethoxysilane (HDTMS) to obtain hydrophobicity. Performance analysis was done by measuring the contact angle of water on the treated fabric surface. The chemical structure, morphology and surface roughness of treated fabrics were characterized by FTIR, SEM and AFM, respectively. Acetate fabrics with good hydrophobicity were obtained when treated with water glass and HDTMS. Such surfaces were obtained first by dip-coating the silica hydrosols prepared via hydrolysis and condensation of water glass onto acetate substrates, and then by modifying the surface of the silica coating with a non-fluor compound (HDTMS). This study demonstrated that the surface treatment using water glass and HDTMS is an inexpensive method for achieving hydrophobic acetate fabrics.
KEYWORDS:
Hydrophobic; Water glass; Acetate fabrics; HDTMS; Surface
Copy the following to cite this article:
Mirjalili M. Surface Modification of Acetate Fabric with Water Glass and Silane Compounds for Hydrophobicity. Mat.Sci.Res.India;9(1)
|
Copy the following to cite this URL:
Mirjalili M. Surface Modification of Acetate Fabric with Water Glass and Silane Compounds for Hydrophobicity. Mat.Sci.Res.India;9(1). Available from: http://www.materialsciencejournal.org/?p=1159
|
Introduction
The research on superhydrophobic surfaces and the related phenomenon of high contact angles dates back a long time 1-7. Besides, superhydrophobic surfaces with a water contact angle higher than 90° have attracted great attention because of their importance in industrial applications. In general, a superhydrophobic surface can be prepared by combination of the surface lowering the surface free energy and enhancing roughness. So far, various methods have been reported for preparing super hydrophobic surfaces such as lithography 8, electro spinning 9, anodic oxidation 10, electrochemical reaction and deposition 11, etching 12, casting and extruding of polymers 13. Recently, roughened surfaces have been commonly obtained by introducing nano-size particles onto the surface. The nano-size particles can be synthesized easily via the sol–gel method 14. Surface-modifying chemicals of fluorinated silanes 15–19 or alkylated silanes 20–24 have been used to transform the hydrophilic surface of the particles into hydrophobic ones. These methods usually are costly. Therefore, there is a need to find novel materials with high performance and low price.
Water glass, a cheap and common industry product, was used as the precursor to prepare silica sol under acid catalyzed hydrolysis and condensation. In this study, water glass and hexadecyltrimethoxysilane (HDTMS) are used as materials to form hydrophobic surfaces on the acetate fabrics by sol–gel method.
Experimental
Materials
The 100% acetate fabric used, had the wrap density of 26 yarn/cm, the weft density of 22 yarn/cm and the fabric weight of 123.5 g/m2. Sodium silicate solution (water glass) from Fluka Company was employed. Hydrochloric acid (HCl), hydroxide ammonium (NH4OH 25%) and ethanol (C2H5OH 98%) were obtained from Merck Company, and hexadecyltrimethoxysilane (HDTMS) was purchased from Aldrich Company. All chemicals were used as received without any further purification.
Preparation of silica sol
The silica sol was prepared via hydrolysis of sodium silicate solution (water glass). A typical preparation procedure can be described as follows: 10 ml of sodium silicate solution was added into 80 ml of distilled water and stirred at room temperature for 10 min. Then various concentrations of 2 mol/L HCl solution were added dropwise to the sodium silicate solution with stirring to form a silica hydrosol.
Synthesis of silica nanoparticles
The spherical silica nanoparticles were prepared by the modified Stöber method of hydrolysis, dehydration and condensation of HDTMS as a precursor 25. Firstly, a mixture of 0.39 mol HDTMS and 2.35 mol ethanol was prepared, then it was mixed with another mixture of 2.94 mol distilled water, 2.35 mol ethanol and 0.05 mol
NH4OH. Hydroxide ammonium was used as a catalyst to control the particle size and distribution. The synthesis was prepared at 30 °C for 24 h.
Table 1: Summary of the exact formulation and notation for each sample examined in this study
Preparation of hydrophobic acetate fabrics
The acetate fabrics were immersed in the silica hydrosol for 3 min, and then padded with a wet pickup of 70–80%. The specimens were dried at 80 °C for 5 min, rinsed with water, dried at 80 °C for 10 min again. The treated fabrics were then immersed in the ethanol solution of HDTMS for 1, 2 and 3 h. Then, treated fabrics dried at room temperature, and cured at 100, 110 and 120 °C for
Table 2: Data of the water contact angle for each sample examined in this study
1 h in an oven. The exact formation and corresponding notation for each sample examined in this study are summarized in Table 1.
Measuring the contact angle
The water contact angle was measured using an optical video contact angle instrument at ambient temperature. The contact angle (σ) values were taken from five measurements at different positions of the same sample. The contact angle was determined according to the following equation:
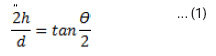
Where h is the droplet height and d is the diameter. h and d was measured using an optical images of the water droplet. The contact angle was determined 0 and 60 second after a water droplet of 5 μl was placed on the acetate substrate.
FTIR analysis
Fourier Transform Infrared (FTIR) spectra were recorded using Shimadzu Infrared Spectrometer in the mid infrared range (450– 4000cm-1).
Surface morphology
The morphology of the treated and untreated acetate fabric was recorded by a scanning electron microscopy (SEM LEO Electron Microscopy Ltd) and Atomic Force Microscope (AFM).
Figure 1: Effect of acid concentration (mL) on contact angle
Results and Discussion
Effective parameter on the contact angle
from the water contact angle results of cured acetate fabric with 9.2, 10, 11.5 and 12 mL of HCL. The obtained results reveal that the water contact angle of the cured samples decrease when the acid concentration increases. It is shown that the average size of the silica particles augmented with the increase of acid. This is because the higher acid concentration accelerated silica sol to condense and silica particles to be aggregated. Fig. 2 show the comparison diagram achieved from the water contact angle results of treated acetate fabric in 100, 110 and 120 °C cured temperatures and Fig. 3 explore the effect of immersed time (h) on the water contact angle of treated acetate fabric. The results show that, by increased the reaction time, the contact angle of acetate treated fabric increases and with increased the cured temperature, the contact angle decreases. Results of the contact angle measurement are presented in Table 2.
Figure 2: Effect of cured temperature on contact angle
Figure 3: Effect of immersed time on contact angle
Structural information
In order to investigate the changes in the chemical structure of acetate fabrics after surface treatment, FTIR spectra of untreated acetate fabric and treated acetate were recorded, and corresponding curves are shown in Fig. 4.
Fig. 5 reveal that surface modification was carried out by replacing H from the surface Si–OH groups by Si–(CH3)3 groups present in HMDS that shows in 800 cm-1, 1600 cm-1 and 3000 cm-1. In 1000cm-1 indicated Si-O-Si groups of condensation water glass and HMDS, it has a crosslink with fabric surfaces.
Surface morphology
The effect of surface roughness on wettability is explained by Wenzel’s equation.
Cosθw = rCos θy …(2)
Where θw is the apparent contact angle on a rough surface, θy is the ideal contact angle on a smooth surface, and r is the roughness factor, which is defined as the ratio of actual area of liquid–solid contact to the projected area. Since r is always larger than 1, this equation indicates that the contact angle will increase with increasing roughness of a hydrophobic surface.
Figure 4: FTIR spectra of (a) untreated acetate surface and (b) acetate surface treated with HDTMS and water glass.
Figure 5: SEM images of (a) untreated acetate surface and (b) acetate surface treated with HDTMS and water glass.
Figure 6: AFM micrographs of (a) untreated acetate surface and (b) acetate surface treated with HDTMS and water glass.
Fig. 5 and Fig. 6 represented SEM images and AFM images of untreated sample and acetate fabrics treated with HDTMS and water glass, respectively. Acetate treated surface (Fig. 5b and Fig. 6b) apparently showed higher roughness than untreated one (Fig. 5a and Fig. 6a). The contact angles of pristine fabric and samples only treated with water glass or HDTMS were not measurable, due to rapid absorbance of falling water droplets.
Conclusion
We have presented a simple method of fabricating hydrophobic surface on acetate substrates with an inexpensive and ordinary raw material, water glass and a non-fluorinated alkylsilane. The fabrics treated with silica sol and HDTMS showed excellent hydrophobic properties, and the water contact angle could reach 131.28 °C. Accordingly, this result implies that this novel technique introduce a variety of potential applications for various substrates with excellent hydrophobicity.
References
- Barthlott W. and Neinhuis C., Planta, 202: 1 (1997).
CrossRef
- Neinhuis C. and Barthlott W., Annals of Botany, 79: 667 (1997).
CrossRef
- Otten A. and Herminghaus S., Langmuir, 202: 405 (2004).
- Wagner T., Neinhuis C. and Barthlott W., Acta Zoologica, 77: 213 (1996).
CrossRef
- Watanabe K. and Udagawa H., AIChE J., 47: 256 (2001).
CrossRef
- Shang H. M., Wang Y., Limmer S. J., Chou T. P., Takahashi K. and Cao G. Z., Thin Solid Films, 472: 37 (2005).
CrossRef
- Hsieh C. T., Wu F. L. and Yang S. Y., Surf. Coat. Tech., 202: 6103 (2008).
CrossRef
- Pozzato A., Dal Zilio S., Fois G., Vendramin D., Mistura G., Belotti M., Chen Y. and Natali M., Microelectronic Eng., 83: 884 (2006).
CrossRef
- Jiang L., Zhao Y. and Zhai J., Angew Chem. Int Ed., 43: 4338 (2004).
CrossRef
- Tsujii K., Yamamoto T., Onda T. and Shibuichi S., J. Colloid. Interf. Sci., 208: 287 (1998).
CrossRef
- Zhang X., Shi F. and Yu X., J. Am. Chem. Soc., 126: 3064 (2004).
CrossRef
- Kim S. H., Kim J. H., Kang B. K. and Uhm H. S., Langmuir, 21: 12213 (2005).
CrossRef
- Feng L., Li S., Li H., Zhai J., Song Y., Jiang L. and Zhu D., Angewandte Chemie, 114: 1269 (2002).
CrossRef
- Huang H. H., Orler B. and Wilkes G. L., Macromolecules, 20: 1322 (1987).
CrossRef
- Okudera H. and Hozumi A., Thin Solid Films, 434: 62 (2003).
CrossRef
- Yan L., Wang K., Wu J. and Ye Lin., Colloid Surf. A: Physicochem Eng, Aspects., 296: 123 (2007).
CrossRef
- Sun C., Ge L. and Gu Z., Thin Solid Films, 515: 4686 (2007).
CrossRef
- Pilotek S. and Schmidt H. K., J. Sol–Gel Sci. Technol., 26: 789 (2003).
CrossRef
- Yang H. and Deng Y. J. Colloid Interface Sci., 325: 588 (2008).
CrossRef
- Bhagat S. D., Kim Y. H. and Ahn Y. S., Appl. Surf. Sci., 253: 2217 (2006).
CrossRef
- Chen L. J., Chen M., Zhou H. D. and Chen J. M., Appl. Surf. Sci., 255: 3459 (2008).
CrossRef
- Xiu Y., Hess D. E. and Wong C. P., J. Colloid Interface Sci., 326: 465 (2008).
CrossRef
- Smitha S., Shajesh P., Mukundan P., Nair T. D. R. and Warrier K. G. K. Colloid Surf. B: Bio interface, 55: 38 (2007).
- Daoud W. A., Xin J. H. and Tao X. M., J. Am. Ceram. Soc., 87: 1782 (2004).
CrossRef
- Stöber W., Fink A. and Bohn E., J. Colloid Interface Sci., 26: 62 (1968).
CrossRef

This work is licensed under a Creative Commons Attribution 4.0 International License.